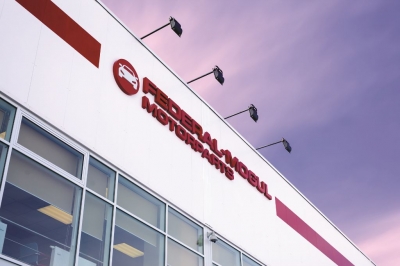
Considerand piata romaneasca atractiva din punct de vedere al costurilor si al nivelului de pregatire a fortei de munca, producatorul american de componente auto Federal-Mogul, care detine in prezent o fabrica de placute de frane si o alta de stergatoare la Ploiesti, nu are in plan vreo incetinire sau stopare a investitiilor din Romania. Ca urmare, a fost demarata deja extinderea unitatii de productie Federal-Mogul Braking cu 50%, compania focusandu-se in acelasi timp pe sustenabilitate si pe imbunatatirea proceselor si sistemelor implementate, dar si pe modalitati de a obtine calitate, defecte 0 si excelenta 5S.
Cu prilejul unei vizite la fabrica de placute de frana am putut remarca nu numai tehnologiile noi, performante, ce pot depasi cu usurinta nivelul celor din Occident, ci si un flux de productie bine planificat, la exactitatea caruia pun umarul atat departamentul de supply-chain, cat si cel de transport, sectoare care folosesc cele mai noi metode, structuri organizationale si procese.
Federal-Mogul Braking detine la Ploiesti o suprafata totala de 70.000 m2. Aici, incepand cu 2012, sunt produse placute de frane pentru vehicule usoare (LV) si vehicule comerciale grele (CV), canalele de distributie fiind OE, OES si after-market (AM). „Zona de after-market este ca o mare organizatie avand la Bucuresti unul din punctele cheie. Fabrica pentru placute de frana de la Ploiesti are peste 300 de angajati, din care o parte sunt dedicati activitatii de logistica, incluzandu-i aici si pe cei care se ocupa de stocuri.
Unitatea de productie de brate si lamele pentru stergatoare detine la Ploiesti un teren de 48.000 m2, din care 12.490 m2 acoperiti. Canalele de distributie a produselor sunt de multe ori similare cu cele ale unitatii pentru placute de frana. Chiar daca in aceasta locatie fabricatia a fost demarata abia in 2015, unitatea are deja in prezent peste 300 de angajati.
Ambele centre de la Ploiesti au fost construite si dezvoltate de la zero, ajungand in prezent sa fie certificate ISO TS 16949 si ISO 14001. De asemenea, fabrica pentru placute de frane detine si certificare OHSAS 18001, in vreme ce unitatea pentru stergatoare se afla in asteptarea obtinerii acesteia.
Federal-Mogul Corporate din Bucuresti are peste 140 de angajati in functii globale precum vanzari, marketing, finante, achizitii, HR, calitate s.a.
O piata inca avantajoasa
Federal-Mogul a ales sa produca la Ploiesti, intr-o zona atractiva pentru investitorii straini din diverse domenii, precum oil&gas (OMV-Petrom, Lukoil, Shell Gas, Cameron, GE – Lufkin, Schlumberger), automotive (Yazaki, Johnson Controls, CalsonicKansei, Michelin), retail (Carrefour, Metro, Selgros, Kaufland, Praktiker, Lidl, Billa, Real) si altele, precum Toro, Timken, Coca Cola, Bergenbier, British American Tobacco, Unilever, P&G. „Avem si avantajul apropierii de Bucuresti, de unde putem aduce angajati specializati. De asemenea, Ploiesti este situat pe unul din cele doua coridoare principale care leaga Romania de Occident si este relativ aproape de Portul Constanta, chiar daca acesta este utilizat in proportie relativ mica“, a punctat Mihai Coroi, manager de transport Corporate EMEA, subliniind ritmul de dezvoltare mult mai accentuat si agresivitatea superioara in sens pozitiv a altor porturi din regiune, in special Koper in Slovenia, dar si a porturilor din Grecia si Bulgaria, pe langa preferinta multor parteneri de a utiliza porturile „clasice“ din vestul Europei precum Hamburg/Bremerhaven, Anvers sau Rotterdam.
Reprezentantul producatorului apreciaza in Romania eficienta costurilor, datorata, pe de o parte, echiparii fabricii cu noi tehnologii, performante, iar pe de alta, costurilor de productie inca mai joase, precum si personalului bine calificat si flexibilitatii acestuia. „Diferentele de costuri dintre productia in Romania si cea in alte tari scad de la an la an. Oricum, este nerealist sa vorbim de o comparatie la nivel de salariu nominal intre diverse tari, mai degraba trebuie sa vorbim despre venituri si corelarea lor cu preturile de pe fiecare piata in parte.
In Romania s-au facut investitii masive
La Ploiesti sunt fabricate anual peste 10 milioane de placute de frane pentru vehiculele usoare si peste un milion pentru vehiculele comerciale mari. Printre clientii importanti mentionam, pentru distributie OEM, TRW, Continental Teves, Brembo, Continental si Bendix, pentru distributie OES, Volvo, PSA, Renault si Daimler, si pentru after-market Scania, DAF, MAN, Iveco si Daimler (Actros).
Fabrica de placute de frane lucreaza cu procese standardizate in toate zonele, utilizand acelasi model logistic in fiecare din unitatile de productie ale Federal-Mogul. „Lucram zi de zi pentru a optimiza si sustine procesele in vederea imbunatatirii calitatii si livrarii, astfel incat sa raspundem asteptarilor clientilor nostri. Este adevarat ca exista o serie de reguli la nivel de corporatie, dar si reguli locale, in functie de specificul zonei“, a explicat managerul de transport. El a mai spus ca principalul avantaj al acestei fabrici din Romania vine din faptul ca este cea mai noua si cea mai moderna dintre unitatile de productie, cu investitii semnificative in tehnologie. Trebuie judecat intreg tabloul, nu doar productia, ci si serviciile de suport, care sunt in crestere in Romania.“
Dupa productie, zona de supply-chain are o importanta deosebita, deoarece sprijina o mare parte din procesele din fabrica. „Cu ajutorul nostru se poate produce la timp, in cantitatea si la calitatea corecta. Este important modul in care gestionam, adaptam si imbunatatim procesele“, a precizat Anda Madotto, SC manager. In departamentul pe care il conduce lucreaza angajati care se ocupa de planificare (relatii cu clientul, planificarea furnizorilor, legatura cu cei care se ocupa cu aprovizionarea cu materiale pentru a evita stoparea productiei, planificarea productiei), dar si de logistica (logistic manager si operatori care se ocupa de incarcarea/descarcarea camioanelor si de furnizarea catre productie a materialelor potrivite.
100% KPI la livrarea just-in-time
In general, unitatile fabricate la Ploiesti merg catre export (80% in Europa, dar si catre USA/Mexic si China), expedierile fiind o responsabilitate a clientilor, uneori fiind utilizata si calea maritima, via Hamburg. De cealalta parte, aprovizionarea cu materii prime se face din Europa, din tari precum Italia, Germania, Spania, Franta, Anglia, Ungaria, Romania etc. Materiile prime sunt complexe si diversificate, de la produse chimice la placi suport din otel, ambalaje si accesorii, furnizorii fiind selectati pe criterii de calitate si cost. „Costurile reprezinta un criteriu important in orice proces de selectie, insa nu vom face niciun rabat de la calitate.“
Modul de ambalare a produselor este ales in functie de cererile/materialele clientului si de complexitatea/fezabilitatea paletilor stivuibili. „Utilizam diferite tipuri de materiale pentru ambalare, precum carton, plastic sau lemn, in ideea de a optimiza costurile si de a asigura o livrare sigura.“
Federal-Mogul Braking Plant lucreaza cu peste 100 SKU (piese finite ce vor fi livrate catre clienti), insa numarul acestora este in continua extindere. „In interiorul fabricii avem foarte multe SKU. Pe de alta parte, avem si volume mari de executat“, a subliniat managerul de SC, punctand ca sunt detinute si produse pe stoc, chiar daca nu pentru o perioada lunga de timp. „Ceea ce se produce in principal pentru clientii mari sta pe stoc in medie cinci zile, deoarece in industria automotive avem variatii foarte mari ale cererilor venite de la clienti, si suntem mandri ca avem 100% KPI la livrarea just-in-time. De asemenea, cream stocuri cand ne pregatim de vacanta, asa cum se intampla vara. In aceasta perioada, pentru livrare folosim unul din furnizorii 3PL.“
Solutii moderne pentru productie, dar si pentru implicarea angajatilor
In ceea ce priveste digitalizarea fabricii, inca din 2012 s-a instalat sistemul SAP, apoi in 2014 KanBan, anul urmator devenind complet functional sistemul propriu, ANDON, in care sunt cuprinse toate informatiile, pornind de la eficienta liniei, pana la actiunile angajatilor, cu vizibilitate non stop asupra statusului productiei si a numarului de oameni din interiorul fabricii. De asemenea, dupa ce in 2015 se atinsese faza 5/7 a Sistemului de Operare, in februarie 2017 fabrica Federal-Mogul devine prima unitate de productie certificata FMOS Bronze, similar cu Certificarea Sistemului de productie Toyota, cel mai inalt grad de certificare existent. „Certificarea arata o dezvoltare continua si sustinuta, constituind astfel un exemplu pentru toate fabricile producatorului“, subliniaza Anda Madotto.
Aceasta a aratat ca planningul productiei se face prin intermediul cardurilor KanBan, in vreme ce solutia Waterspider este destinata operatorilor, respectiv zonei de SC care are nevoie sa aduca materialul din depozit in zona de productie. „Exista o serie de constrangeri de care trebuie sa tinem seama in momentul in care facem planificarea productiei. Timpul de productie depinde de aplicatie, de volum si de disponibilitatea masinilor“, a mai spus managerul de SC.
Pentru angajati se organizeaza regulat traininguri si se promoveaza relatiile pozitive (PER), pentru toate nivelurile. De asemenea, a fost implementat sistemul Value Stream organization, intalniri la nivel de management si nu numai, in fiecare dimineata, in interiorul fabricii. Zilnic, exista un program de training, fie pe teme de calitate, fie de ambalare, siguranta sau procese. In plus, angajatii pot, prin intermediul filosofiei Kaizen, sa propuna imbunatatiri ale modului de lucru, care se pot pune in practica. Mai mult, expertii interni de SSM ofera zilnic instruiri privind securitatea, dar exista si instruiri de tip talent management si coaching.