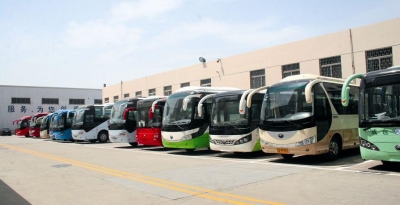
In perioada Busworld Asia, Yutong a oferit jurnalistilor europeni din presa de specialitate ocazia de a vizita o parte a fabricii din Zhengzhou: atelierele destinate sasiurilor si asamblarii finale, statiile de galvanizare a sasiului si a caroseriei si centrul de testare. Intregul complex ocupa o suprafata de 1,12 milioane de hectare, iar in curand parcul industrial va fi extins si se va ajunge la 50.000 de autobuze/autocare fabricate pe an, cifra aproape dubla fata de cea din prezent.
Yutong este cel mai mare producator chinez de autocare si autobuze medii si mari si ofera o gama larga de vehicule, de la 6 la 25 m lungime, grupate in 35 de familii si 98 de serii, destinate transportului public, tranzitului pe autostrada sau turismului.
Cu 28.126 de autobuze si autocare vandute in 2009 si o cota de 7-8% din piata de vehicule nou inmatriculate (22% in China, unde este lider), Yutong este cel mai mare producator din lume dupa Daimler (32.482 de unitati), fiind urmat la distanta destul de mare de Marcopolo, Higer, Volvo si MAN. In 2009 a avut o cifra de afaceri de 15,03 miliarde RMB (un euro echivaleaza cu aproximativ 9 RMB), fata de 14,08 in 2008, cand s-au vandut 27.556 de vehicule. Asadar, producatorul chinez si-a mentinut cresterea in 2009, in ciuda crizei economice, iar acest lucru se datoreaza, asa cum declara reprezentantii firmei, retelei puternice de service si marketing.
Autobuzele Yutong aflate in prezent pe piata parcurg 24,5 miliarde de kilometri si transporta circa noua miliarde de pasageri pe an.
Grupul Yutong produce si piese de schimb si utilaje de constructii si este implicat si in dezvoltari imobiliare.
Tehnologie de varf, importata de la firme de renume
Atelierul de producere a sasiurilor a adoptat modelul Toyota Lean Management, care a permis standardizarea operatiilor si imbunatatirea calitatii si a eficientei. Suprafata este impartita in patru, in functie de natura operatiilor: galvanizare, sudura, asamblare si inspectie.
Echipamentul de galvanizare a sasiurilor provinde de la Paccar, are o capacitate de 130 de sasiuri/zi si este controlat automat, astfel ca nu necesita decat prezenta a patru oameni. Procedura presupune 16 pasi, de la curatarea suprafetei pana la vopsirea propriu-zisa, prin electroliza.
Atelierul de galvanizare a caroseriei a fost realizat in colaborare cu Dürr, de la care a fost achizitionata tehnologia, si este unul dintre cele mai avansate din lume (doar cinci producatori de autobuze folosesc cataforeza, asa cum declara reprezentantii Yutong), cu control in mare parte automat. Si aici este vorba de 16 pasi si se poate lucra simultan la patru vehicule, rezultand aceeasi capacitate de 130 de unitati/zi.
Datorita tratarii cataforetice a sasiului si a caroseriei, Yutong ofera o garantie anticoroziune de opt ani.
Am fost apoi condusi spre doua dintre liniile de productie a sasiurilor – in total fabrica are opt, cu o capacitate de 130 de unitati/zi. Pe fiecare dintre ele se executa 16 operatiuni (deci se lucreaza simultan la 16 sasiuri) care necesita, in functie de complexitate, cate 10-20 de oameni. Autobuzele mari se misca in noua minute de la un post de lucru la altul, iar cele medii, in sase minute.
Dupa ce toate componentele sunt montate pe sasiu se fac teste, iar daca rezultatele sunt bune se merge pe linia de asamblare.
De aceasta data este vorba de 15 operatii pe fiecare din cele sase linii, din care patru pentru vehicule de peste 10 m, una pentru autobuze scolare si una pentru autocare double decker.
Laborator unic in China
Centrul de testare este una dintre cele mai noi si mai moderne componente ale fabricii Yutong – tocmai de aceea folosirea camerelor foto a fost interzisa – si include mai multe departamente, care se ocupa de designul autobuzelor hibrid, masurarea zgomotului, a vibratiilor, a consumului, simularea mersului pe sosea (manevrabilitate, confort la rulare si durabilitate), de echipamentele electronice, uzura materialelor si validarea designului.
Primele camere prin care trece un nou vehicul sunt cele in care se verifica etanseitatea, comportamentul la lumina soarelui, timp de 24 de ore, usile, la 600 de cicluri de inchidere/deschidere, si temperatura – functionarea luminilor sau a DVD-playerelor este testata de la -70 la +130oC. Urmeaza examinarea durabilitatii structurii. Initial, aceasta se facea prin teste de impact si de rasturnare, dar in prezent se apeleaza doar la simulari pe calculator, in 20 de zile fiind „atinsi“ 20 de milioane de kilometri de mers pe sosea, adica aproximativ 10 ani de utilizare a vehiculului in China. Este un aspect caruia Yutong ii acorda o mare importanta, astfel ca autobuzele/autocarele sale corespund standardelor europene ECE R66.
Deoarece Yutong se ocupa pe cont propriu de designul autobuzelor/autocarelor, are propriul laborator unde sunt verificate parti ale vehiculelor ce urmeaza sa fie lansate.
Testele pentru scaune vizeaza functionarea centurii de siguranta, comportarea la impact si rezistenta materialului. Pentru asta se simuleaza mersul pe drumuri accidentate, acelasi echipament fiind folosit si pentru verificarea durabilitatii boghiului.
Urmeaza calibrarea directiei si noi teste in timpul carora se simuleaza conditiile de drum, inclusiv cu vibratii si zdruncinaturi, vehiculul fiind incarcat la capacitate. Echipamentul este folosit de fiecare data cand apare un model nou si se adapteaza si la autobuzele cu doua axe, si la cele cu trei.
Urmeaza testarea suspensiilor, cu o masina despre care gazdele noastre ne-au spus ca este deocamdata unica in China, a doua urmand sa fie achizitionata in curand de Mercedes.