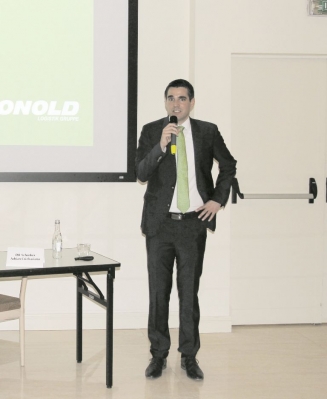
Desi vehiculele produse si asamblate in Romania au depasit 387.300 de unitati in 2015, in scadere cu 2014 fata de anul anterior, piata romaneasca de automotive inca ramane extrem de ofertanta pentru furnizorii de servicii logistice. Insa logistica din automotive este extrem de complexa, la fel ca cea din farma sau distributia FMCG, presupunand procese complexe atat in zona de productie, cat si in cea de logistica. Iar partea cea mai dificila vine nu numai din livrarile intr-o anumita fereastra fixa de timp, astfel incat sa nu se creeze nici congestii, dar nici oprirea liniilor de productie, cat si dintr-o secventare exacta a produselor livrate.
Mai mult, domeniile in care se foloseste logistica au ajuns sa treaca dincolo de cele traditionale ca transport, expeditie sau depozitare, industria automotive solicitand in plus un nivel de automatizare si investitii in tehnologie cat mai ridicate, dar si standardizari si analize amanuntite ale riscurilor.
Sectorul logistic din automotive este inovativ si extrem de dinamic, astfel incat orice furnizor de servicii din acest segment are nevoie de abordari noi precum livrari just-in-time (JIT) si just-in-sequence (JIS), dar si de integrarea unui numar mai mare de furnizori, investitii in cladiri si depozite multi-user, in consolidare de bunuri si sisteme informatizate. „Cerintele moderne ale logisticii automotive se bazeaza din ce in ce mai mult pe investitiile in servicii cu valoare adaugata“, a punctat reprezentantul companiei germane Honold Logistik Gruppe, Lukas Maier.
Timpii de livrare si analiza riscurilor, puncte cheie
Reprezentantul companiei germane este de parere ca furnizorii de logistica trebuie sa respecte anumite cerinte tipice lucrului in industria automotive astfel incat sa corespunda solicitarilor de calitate ale clientilor. Intre cerintele de baza, Maier a precizat certificarea DIN ISO 9001, DIN ISO 14001, DIN ISO 16949, respectarea regulilor de siguranta in operare, proceduri de operare cu documentatie standard, personal calificat si o dezvoltare continua a angajatilor. Acestora li se adauga, pentru o comunicare corecta intre conducerile companiilor: procese cu standardizare si transparenta ridicate, proceduri sistematice si documentate pentru sarcini preventive si corective, imbunatatire continua, analize ale riscurilor, raportari privind performanta, auditarile clientilor si implementarea tehnicilor de calitate specifice in automotive, precum Raportare-8D, FMECA, Lean Management sau 5S. „Furnizorul de servicii logistice trebuie sa se focuseze in special pe analiza riscurilor, destul de prezente in sectorul automotive, in special pe cele care privesc siguranta, costurile si marketingul, dar si pe instrumentele de calitate proprii companiilor, la care logisticianul trebuie sa se adapteze.“
De asemenea, volatilitatea pietelor automotive si necesitatea unor timpi rapizi de raspuns necesita adaptabilitate si flexibilitate sporite ale furnizorului de servicii logistice. „Acesta trebuie sa utilizeze depozite multi-user, sisteme IT inteligente care sa vina in sprijinul proceselor de operare. Nu mai este de ajuns sa ofere doar transport si depozitare, ci este nevoie din ce in ce mai mult de servicii cu valoare adaugata“, a explicat Lukas Maier, mentionand aici sisteme IT specifice fiecarui client sau manipularea si urmarirea unui numar mare de paleti diferiti, specifici domeniului automotive. In plus, e nevoie ca distantele pana la fabricile clientilor sa fie reduse, astfel incat sa poata oferi timpi cat mai rapizi de raspuns. „In functie de zona, apelam la diferite strategii. Astfel, avem clienti pentru care facem distributie dedicata cu masini proprii, fie ca sunt dealeri sau clienti ai clientilor nostri, dar sunt cazuri in care, pentru flexibilitate si costuri corespunzatoare, apelam si la subcontractori.“
Strategii diferite, in functie de piete
Pentru ca logistica din automotive presupune investitii considerabile, este nevoie de o productivitate cat mai mare pentru a obtine rezultate acoperitoare. Ca urmare, se impun preturi extrem de competitive, procese de licitatie standardizate, strategii de achizitii sustinute de instrumente de reducere a costurilor (licitatii online, e-licitatii), optimizari continue si penalitati contractuale pentru lipsa de calitate si performante scazute. De cealalta parte, exista si clienti din automotive care au cerinte foarte specifice in contracte privind plata unor penalitati mari, adesea care depasesc castigul, pentru intarzieri in livrare. „Ne-am confruntat cu asta si in Germania. Conditiile sunt foarte stricte din cauza costurilor foarte mari pentru neconformitati. Se considera ca in fiecare etapa din supply-chain costurile pentru erorile nedetectate se multiplica de zece ori“, a mai spus Lukas Maier.
In Romania, din 2005, compania germana este prezenta printr-un joint-venture cu Karl Heinz Dietrich, in toti acesti ani reusind sa investeasca impreuna si sa realizeze operatiuni in centrul de distributie de 20.000 m2 din Sacalaz (Timis), extins in urma cu trei ani cu inca 10.000 m2, precum si in depozitul de 40.000 m2 al unei fabrici din domeniul automotive din Timisoara. „Joint-venture-ul Dietrich-Honold Logistics imbina doua competente: cea detinuta de grupul Honold, care, beneficiind de know-how si experienta, a castigat clientul, si cea a companiei Dietrich, care cunostea foarte bine piata de logistica romaneasca“, a punctat Lukas Maier.
De asemenea, acesta a aratat ca automatizarea Honold din Sacalaz nu este la acelasi nivel cu cea cu care lucreaza in Germania, insa se afla si aici in plin proces de modernizare. De exemplu, s-a trecut de la incarcarea manuala la cea automatizata, cu conveioare.
Maier a subliniat ca o parte importanta a cifrei de afaceri a Honold Logistik Gruppe era obtinuta inainte de criza numai din industria automotive, insa situatia dificila a pietei din 2008-2009 a dus la o reorientare catre zone noi de business, cum ar fi cea farmaceutica sau industria high-tech.
31% din cifra de afaceri a DB Schenker vine din automotive
In Romania, DB Schenker, care are 60 de birouri cu cinci sucursale majore, sase centre logistice insumand 35.000 m2 si aproximativ 1.000 de angajati, obtine din automotive, pe diversele segmente de transport, 31% din cifra de afaceri de 100 de milioane de euro in 2015. „Operatorul privat de cale ferata Schenker Rail lucreaza predominant cu Ford. In fiecare zi avem circa 250 de trenuri fixe care ruleaza in Europa numai pentru industria auto, atat pentru vehicule finite, cat si pentru partea de componente. De asemenea, efectuam circa 100.000 de expeditii/ an cu camioane complete in acest domeniu, iar 1,7 milioane m2 din cele 7-8 milioane m2 de spatii logistice la nivel mondial sunt dedicate acestui segment (25%). Practic «atingem» productia a 6.000.000 de vehicule anual prin ceea ce facem noi pe diverse segmente“, a punctat Adrian Crizbasianu, Chief Operating Officer la Schenker Logistics Romania.
Acesta a mai precizat ca in Romania operatorul inregistreaza cel putin 10.000 de declaratii vamale anual legate de acest segment de activitate (10% din total). Desi transportul in regim de grupaj totalizeaza circa 3.000 de expeditii, partea majoritara a activitatii rutiere din automotive provine din cele 30.000 de transporturi complete realizate anual. „De sase ani acoperim un flux de componente pre-productie de la Mioveni catre diverse fabrici auto din grupul Renault“, a punctat Crizbasianu, mentionand ca anul trecut circa 2.200 t de marfa a fost transportata pe cale aeriana.
DB Schenker a desfasurat in 2015 o campanie intensa pe automotive in Romania, cautand solutii logistice integrate si aspecte care sa releve unde poate sa intervina operatorul de logistica in toate aceste fluxuri, pornind de la furnizori si terminand cu automobilele noi, iar in mijloc fiind partea de productie, fabrica si huburi de consolidare. „In aceste lanturi putem forma pre-huburi in care colectam componentele de la diversi furnizori, ce vor fi transferate apoi intr-un hub central sau direct intr-o unitate de productie de automotive. Am luat in considerare si varianta in care exista un pre-hub de consolidare in proximitatea furnizorilor, apoi livrarea pe cale aeriana, rutiera sau feroviara catre aceste unitati de logistica mai mari unde se pot desfasura operatiuni cu valoare adaugata: sortare, control de calitate, schimbare din ambalajul de transport in cel de productie. Apoi se face livrarea catre unitatea de productie a furnizorului, la final rezultand autovehiculul in stare completa ce va necesita transportul catre pietele de destinatie“, a detaliat Adrian Crizbasianu, subliniind prezenta DB Schenker in toate aceste lanturi. „Incercam sa facem si in Romania cat se poate din toate aceste lucruri.“
Proiecte de tip win-win
In cadrul ExpoTranzit, Schenker Logistics Romania a prezentat si cateva studii de caz. Unul dintre proiecte, initiat in 2013 in Constanta, pe o suprafata de depozitare de 1.000 m2, pentru un furnizor de jante (circa 220.000 de bucati anual), destinate in special pentru gama Dacia Duster, presupunea primirea bunurilor livrate in containere din Asia, descarcarea acestora, control vizual de calitate/bucata, reambalare conform specificatiilor de la Mioveni pentru linia de productie si pastrarea intr-un antrepozit vamal din interiorul Portului. Apoi se faceau livrarile catre fabrica de la Mioveni, urmand pasii necesari, de la trasabilitate si vamuire la etichetare, potrivit specificatiilor. „La final, producatorul de autoturisme nu importa direct jantele, ci le primeste doar atunci cand are nevoie de ele, fara sa mobilizeze partea de capital mai devreme de doua zile inainte de primirea in linia de productie“, a precizat Crizbasianu. Acesta a mentionat un al doilea proiect, pentru acelasi flux, locat tot in Constanta, insa la un nivel mai mare: 350.000 de anvelope anual. „Se poate ca la un moment dat sa facem si partea de asamblare, direct in Constanta, dat fiind faptul ca de cele mai multe ori anvelopele si jantele vor merge cu aceeasi masina.“
Un alt caz se refera tot la parti de pre-productie destinate unui producator de componente auto. Astfel, o serie de furnizori livreaza produsele catre depozitul Schenker din Arad unde, fluxul fiind mare, se lucreaza in trei schimburi, inclusiv sambata. „Zona Arad e o mare provocare din punct de vedere al fluctuatiei si al costului fortei de munca. Iar in momentul in care desfasori operatiuni in trei schimburi, 6/7 zile, lucrurile pot sa se complice destul de repede“, a spus Crizbasianu, completand: „preluam toate aceste parti si, daca este nevoie, desfasuram operatiuni aditionale, control de calitate, sortare, reambalare, dupa care livrarile se fac conform comenzilor primite prin sistemul automotive al clientului. Avem un sistem de shuttle, la fiecare patru ore trei camioane plecand de la depozitul nostru catre aceasta unitate de productie a clientului.“ In mod similar, in acelasi depozit operatorul lucreaza pentru un alt producator de componente, tot din zona, care are trei fabrici ce trebuie aprovizionate. „Luam componentele pre-productie si le stocam in depozit, dupa care avem noua livrari/zi catre lanturile de productie. De asemenea, avem si un flux invers: o parte din produsele finite pe care le produc se intorc in depozitul nostru, dupa care se face livrarea direct catre Daimler si alte fabrici de autoturisme din Europa.“
„Just-in-sequence“ inseamna mult mai mult
La Craiova, din 2012, Schenker a semnat un contract cu un producator de cablaje pentru servicii de logistica la fabrica, unde, pe cei 2.000 m2 in care se primesc bunurile, se fac operatiuni de sortare si control de calitate. „Fata de modelele anterioare, aici este vorba de o livrare direct pe linia de productie a Ford, caz in care trebuie sa se respecte livrarea JIS, nu doar JIT. Asta inseamna ca daca trebuie livrate 10 cablaje auto pentru 10 masini care urmeaza a fi produse in functie de o anumita specificitate, acestea nu trebuie doar sa ajunga la timpul stabilit, ci si secventate corect, astfel incat lucratorul de la banda sa nu mai fie nevoit sa verifice daca acel cablaj e potrivit cu modelul“, a mai spus Adrian Crizbasianu.
Pe segmentul after-market, Schenker opereaza un model de distributie de piese de schimb pentru un brand cu centrul logistic principal in Köln, Germania. Daca este nevoie de o anumita componenta pentru o masina, se lanseaza comanda astfel incat in maximum 2-3 zile piesa respectiva sa ajunga direct din Köln, prin intermediul unui sistem de shuttle dintre Köln, Budapesta (ca punct intermediar) si Arad, de unde se face distributia in vestul tarii, sau Bucuresti, pentru sud si est. Acelasi client are insa si un flux invers, toti acesti producatori de componente din Romania solicitand un sistem de preluare consolidata a componentelor si livrare catre acel hub central din Germania.
„Toate fluxurile pe partea de logistica – livrari de la depozit catre linia de productie – au la baza un sistem mult mai bogat decat un WMS obisnuit, cel mai degraba bazat pe un sistem SAP, fie al Schenker, fie al clientului. In baza acestui sistem si a etichetelor specifice din automotive se poate vedea instantaneu, prin scanare, la iesire din doc la noi, sau la intrare in doc la productie, daca s-a livrat altceva decat s-a comandat. In caz de discrepante se declanseaza o procedura alternativa, astfel incat piesa care poate lipseste sa fie transferata in regim de urgenta“, a mai precizat Adrian Crizbasianu.