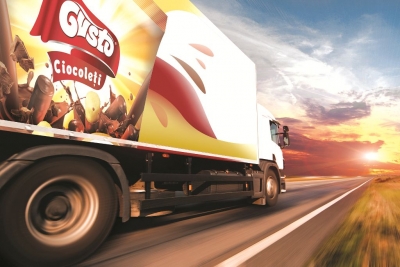
Compania Phoenixy, care produce pufuletii Gusto de mai bine de 20 de ani, se bucura azi, pe de o parte, de o prezenta evidenta pe rafturile tuturor magazinelor romanesti si in casele familiilor cu copii, si nu numai, iar pe de alta, de o apreciere binemeritata la export, circa 40% din cele peste un milion de pungi produse in fiecare zi ajungand pe rafturile marilor retaileri internationali precum Spar, Aldi, Carrefour, Auchan, Rewe, Metro sau Edeka.
Insa etapele de trecere de la un expandor montat in subsolul unei case la o fabrica de peste 30.000 m2 si depozite proprii de 10.000 m2, realizate prin investitii proprii, pentru o expansiune cat mai sanatoasa, nu au fost facile, atentia fiind indreptata in permanenta spre reducerea costurilor si spre investitii in eficienta, pornind de la un service pentru flota proprie si o centrala fotovoltaica instalata pe acoperisul fabricii, pana la crearea propriului departament de standardizari, realizat in colaborare cu Universitatea din Bucuresti.
Povestea pufuletilor Gusto si a companiei Phoenixy incepe in 1992, in Ploiesti. Odata cu cresterea productiei a aparut insa nevoia de relocare a facilitatilor intr-o zona cu caracter industrial si cu potential de extindere, in Baicoi. „Am inceput aceasta companie de la zero, cu un expandor montat in subsolul casei parintesti, si am continuat sa investim, timp de mai bine de doua decenii, intr-o unitate cu o capacitate mare de productie. Nu a fost vorba de o decizie strategica, asa cum se intampla in cazul companiilor multinationale, ci ne-am dezvoltat pas cu pas“, a punctat co-fondatorul si directorul general Phoenixy, Eliodor Apostolescu. „Valoarea investitiei (in terenuri, cladiri si utilaje) se ridica la aproximativ 40 de milioane de euro, realizandu-se treptat, prin reinvestirea profitului companiei, fara utilizarea creditelor de la banci sau a fondurilor europene.“
In prezent, compania pune la dispozitie 186 de coduri de produs, cel mai cunoscut brand pe plan national si international fiind pufuletii Gusto, cu multiple sortimente, intre care si cel mai recent model lansat pe piata, pufuletii Bio. Pe langa pufuleti, compania exporta si piese, componente si echipamente produse de sectia mecanica proprie. „Cresterea productiei a fost accelerata, in cei 20 de ani de activitate reusind sa dezvoltam o tehnologie de fabricatie unica in lume, o fabrica de peste 30.000 m2 si vanzarea produselor Gusto in 20 de tari. Am creat o afacere pur romaneasca, de milioane de euro“, a precizat Eliodor Apostolescu, subliniind ca vanzarile in continua crestere, de la zero la peste un milion de pungi de pufuleti pe zi, au finantat in timp dezvoltarea. „Ne propunem o crestere de aproximativ 20% pe an, desi pare greu de realizat. Insa performantele apar doar atunci cand ai provocari zilnice si iesi din «zona de confort».“
Directorul general a precizat ca cifra de afaceri a companiei prahovene a fost de 18 milioane de euro in 2014, iar anul trecut a ajuns la 17,5 milioane de euro.
40% din productie merge la export
Compania are in prezent 300 de angajati, din care 80 dedicati logisticii si 190 productiei. Fabrica lucreaza la aproximativ 80% din capacitatea disponibila, in trei schimburi. „Datorita volumului urias ocupat de produse, nu putem face stocuri. In plus, ne dorim sa livram produse proaspete catre clienti“, a punctat Apostolescu. Acesta a explicat ca vanzarile maxime se realizeaza in perioada rece, cu scaderi de maximum 20-25% in perioada verii, atunci cand alimentele sarate sunt mai putin cautate. Ca urmare a faptului ca vara oricum este perioada concediilor, este redusa si capacitatea de productie prin oprirea liniilor ai caror salariati sunt in concediu.“
Pe langa exporturile directe, o parte din produsele fabricate de Phoenixy, comercializate in Romania, sunt reexportate, ajungand astfel ca circa 40% din totalul fabricat sa mearga la export, cu mentiunea ca sezonalitatea vanzarilor din Romania coincide cu cea din restul regiunilor in care se exporta. „Cu timpul, balanta dintre export si vanzarile nationale va inclina tot mai mult catre exporturi, aceasta fiind directia strategica principala pe care ne concentram in acest moment“, a aratat directorul general.
Materiile prime utilizate de companie sunt in general de origine agricola, conventionale si organice, procurate atat de la furnizori interni, cat si din strainatate. „In ultimii ani, preturile materiilor prime au oscilat la nivel mondial, per ansamblu inregistrand o usoara crestere. Exista, insa, si materii prime cu fluctuatii mari de pret date de productia agricola globala sau de evolutia tendintelor de consum, ca in cazul arahidelor si migdalelor“, a mai spus Eliodor Apostolescu.
Materia prima este livrata de furnizori cu ajutorul camioanelor, dar si al cisternelor, in functie de specificul materiei prime respective. Apoi, procesul de productie incepe cu selectia acestor materii prime, urmand receptia si fabricatia. „Procesul de pregatire a materiilor prime este la fel de complex ca si productia in sine. Apoi, productia este insotita de un control de calitate permanent, produsele tuturor liniilor de fabricatie fiind analizate la fiecare 20 de minute. Toate acestea sunt urmate de ambalarea si depozitarea produselor.“
Lunar sunt incarcate peste 1.000 de camioane
Langa fabrici compania detine depozite proprii, de 10.000 m2, in care lucreaza 30 de angajati. Acestea sunt echipate cu rafturi de 9 m inaltime, in care produsele sunt asezate ergonomic si organizate pe zone si coduri. Perioada medie in care un produs sta in depozit inainte de a fi livrat este de patru zile, iar pentru o organizare eficienta se utilizeaza un WMS de la Oracle, plus un soft propriu, dezvoltat impreuna cu o echipa din cadrul Universitatii din Bucuresti.
Receptia marfurilor se face pe baza rapoartelor de productie sau a comenzilor lansate catre furnizori, insotite de un proces verbal de receptie calitativa si cantitativa. Ulterior, aceasta primeste un cod de depozitare. „Pentru a reduce furturile, am instalat un sistem de monitorizare video. De asemenea, la incarcarea camioanelor emitem o nota, semnata de sofer si de gestionarul depozitului, care se confrunta, prin sondaj, cu probele video“, a punctat Apostolescu, adaugand: „ne-am confruntat, ca si alte companii, cu furturi. Nu am rezolvat complet aceasta problema, insa prin selectia personalului, o buna conexiune cu angajatii plus monitorizare video, am redus aceste incidente la un nivel nesemnificativ.“ Pe de alta parte, desi compania lucreaza cu paleti la schimb sau factureaza paletii nereturnati, tot inregistreaza circa 15% pierderi ale acestora.
In tara, distributia produselor se realizeaza atat cu camioanele proprii, cat si cu cele ale unor transportatori-colaboratori care, in perioadele de varf, acopera surplusul de livrari. „In conditiile in care sunt incarcate lunar peste 1.000 de camioane, eficientizarea costurilor o realizam printr-o buna mentenanta a flotei proprii, printr-o dispecerizare eficienta, precum si prin acoperirea, la retur, a camioanelor goale“, a aratat directorul general. Acesta a subliniat ca dezvoltarea continua a companiei implica achizitionarea permanenta de utilaje sau camioane, „neexistand niciun an din istoria companiei fara astfel de achizitii“.
Fiecare camion din flota Phoenixy este echipat cu trei sisteme independente de monitorizare, chiar daca cei 60 de soferi sunt instruiti si in firma, prin intermediul departamentului de logistica, si prin cursuri cu instructori specializati.
„Productie mai mare cu 20% fata de 2008, dar cu 25% mai putini salariati.“
Ca producator, compania prahoveana acorda o mare atentie reciclarii, asumandu-si obiectivele reducerii emisiilor de CO2. „In urma cu trei ani am finalizat instalarea unei centrale fotovoltaice, ce reduce emisiile de CO2 cu 450 t pe an. Aceasta a fost realizata dupa o investitie de 900.000 de euro in panouri solare, amplasate pe acoperisul fabricii din Baicoi“, a precizat Eliodor Apostolescu, subliniind ca vor continua investitiile in tehnologie, aparatura si inovatie.
Pe de alta parte, compania investeste in solutii de eficientizare a activitatii, pornind de la masurarea eficientei pe fiecare salariat. „Realizam astazi o productie mai mare cu 20% fata de 2008, dar cu un numar de salariati mai mic cu 25%“, a punctat directorul general, continuand: „atunci cand dezvolti o activitate economica te confrunti permanent cu situatii de criza, fie financiare, fie de personal sau de vanzari. Pe aceste considerente, avem un plan permanent de criza din care au rezultat economii uriase.“ Ca exemplu, acesta a precizat dezvoltarea unui service propriu de camioane, care asigura mentenanta flotei, instalarea centralei fotovoltaice pe acoperisul fabricii, instalarea unei statii de motorina proprii in curtea fabricii si dezvoltarea atelierului mecanic si a departamentului de logistica. In plus, compania intentioneaza sa se extinda, prin construirea unui depozit propriu in Germania.
De asemenea, unul dintre cele mai notabile exemple de inovatie si de crestere a profitabilitatii este crearea propriului departament de standardizari, in care a fost cooptata si o echipa performanta din cadrul Universitatii din Bucuresti. „Prin intermediul acestuia analizam toate procesele din firma, sesizam disfunctionalitatile si cream proceduri specifice care au rolul de a imbunatati sau de a modifica substantial activitatea de productie sau diferite procese interne.“