Digitalizarea și conectivitatea sunt acum redefinite, în condițiile în care companiile își reorganizează activitatea și modul de lucru, în contextul pandemiei. Operatorii logistici și producătorii deopotrivă își doresc să fie mai flexibili și mai puțin dependenți de forța de lucru, iar industria 4.0 și digitalizarea depozitelor reprezintă noua realitate. Trecerea la digitalizare și automatizare nu se poate face însă peste noapte. Tehnologia există, la fel și software-urile pentru a pune în aplicare noile sisteme. Totuși, ritmul de creștere a automatizării în spațiile logistice și de producție nu este la fel de mare pe cât și-ar dori potențialii beneficiari. Cel mai recent seminar online organizat de Still Material Handling a abordat implicațiile automatizării fluxurilor de marfă și procesele și costurile aferente implementării.
Automatizarea devine o opțiune tot mai atractivă, dar și mai accesibilă pentru companiile care activează în logistică, distribuție și curierat. Și în România, reprezentanții Still Material Handling au constatat un interes sporit din partea clienților pentru soluții automatizate, pentru softuri personalizate destinate managementului flotei, dar și pentru echipamente specializate tip VNA, pentru operare pe culoare înguste. „Pe viitor probabil că vom asista mai puțin la lansări de noi echipamente și mai mult la lansări de noi sisteme automatizate și soluții software, menite să crească eficiența. Vedem această tendință deja în Occident, iar Europa de Est va urma în scurt timp”, a declarat Marek Juhas, director general Still Material Handling România.
În același timp, Cristian Cărare, National Key Account Manager, subliniază că sunt câteva proiecte interesante de automatizare și în România, derulate de Dematic, compania din grup care dezvoltă soluții de automatizare, alături de clienți importanți de pe plan local. Unele proiecte sunt deja implementate, altele în stadiu de discuție. „Discuția trebuie purtată până la nivel de detaliu. Din păcate, deși multora le surâde ideea de a automatiza, nu sunt multe companii care să știe cu adevărat ce implică această automatizare. Când ajungi să discuți proiectul intervin semnele de întrebare și încercăm să îi consiliem pe clienți, deoarece o soluție de automatizare nu o implementezi acum și să o schimbi complet în 3-5 ani.”
Nivelul de automatizare va crește până în 2025
Potrivit unui studiu derulat de Still Material Handling în rândul a 500 de clienți din intralogistică din Europa cu privire la perspectivele automatizării parțiale sau complete a proceselor logistice, cei mai mulți dintre respondenți își doresc ca până în 2025 să aibă în depozite o pondere 50-50% între munca manuală și cea automatizată. Mai mult, unii s-au arătat deciși ca, în același interval de timp, să își automatizeze complet procesele în depozit, pentru a avea disponibilitate de lucru 24 de ore pe zi, dar și eficiență crescută în operare. Un alt motiv pentru care companiile tind către automatizare este siguranța. Rămâne însă de văzut câte dintre acestea vor reuși să își atingă obiective atât de ambițioase într-un timp așa de scurt.
În prezent, mai mult de jumătate dintre firmele care au participat la sondajul Still își realizează majoritatea proceselor logistice cu ajutorul angajaților, iar perspectiva automatizării – chiar și într-un procent de 50% – este îndepărtată.
Principalele probleme identificate sunt necesitatea schimbării proceselor și procedurilor complexe de lucru aflate în funcțiune, teama că automatizarea nu a atins un nivel suficient de ridicat de maturitate din punct de vedere tehnologic și că nu se poate adapta la specificul fiecărei aplicații în parte, costul investiției inițiale și imposibilitatea identificării punctului de plecare sau a momentului propice pentru a face schimbarea.
Schimbarea proceselor complexe de lucru
Pentru a arăta cum se pot automatiza și, implicit, eficientiza diferite procese logistice, echipa Still a oferit câteva exemple concrete de utilaje care sunt deja disponibile în variante automatizate. Primul este trenulețul de tractare autonom, care transportă paleți în depozit. Nu doar că utilajul se deplasează singur, ci și paleții sunt încărcați automat pe conveioare, aceștia fiind transportați automat la linia de producție. De asemenea, paleții goi sunt aduși înapoi în depozit, urmând același proces.
A doua aplicație vizează clasicul reach-truck, popular în toate depozitele. În versiunea autonomă, paleții pot fi manipulați și depozitați la înălțime și, foarte important, inclusiv la nivelul podelei se poate realiza o depozitare în „bloc”, întregul proces fiind automatizat.
În cazul depozitelor foarte aglomerate sau în zonele unde chiria pentru spațiul de depozitare este foarte mare se poate opta pentru sistemul de culoare înguste, unde densitatea mărfii este ridicată. Stivuitoarele speciale VNA pot opera și aici complet automat. De regulă, aceste utilaje nu părăsesc culoarele pe care sunt montate. Tocmai de aceea Still a dezvoltat o interfață compatibilă cu un alt utilaj de transport – un stacker, care preia paleții și îi duce la destinație (aceștia pot fi inclusiv așezați la rând, gata pentru a fi încărcați pentru distribuție). Ambele echipamente pot fi conectate grație interfeței comune și pot lucra autonom. În funcție de aplicație, pentru aprovizionarea liniilor de producție se poate opta pentru trenulețul autonom ori pentru stacker.
În cazul proceselor de picuire, Still propune utilajul robotizat neo de ultimă generație, care susține munca manuală. Operatorul poate merge de-a lungul rafturilor, iar echipamentul îl urmează, astfel încât marfa să fie picuită și încărcată cât mai rapid. Acesta este exemplul cel mai relevant de colaborare între om și mașină.
Planificarea și evaluarea implementării automatizării
În momentul configurării unui depozit automatizat trebuie stabilit de la început tipul de marfă manipulată: dimensiuni, greutate, mod de depozitare și de transport. Apoi, sunt importante condițiile de depozitare (temperatură, eventual praf etc.) și tipul de rafturi folosite.
Investiția în automatizare este rentabilă doar dacă timpul de amortizare este suficient de rapid. Cu alte cuvinte, nu orice operațiune merită automatizată. De regulă, în cazul aplicațiilor în care se lucrează în mai multe schimburi, automatizarea este binevenită, iar investiția se recuperează mai rapid.
Nu în ultimul rând, dimensiunea flotei de echipamente reprezintă un factor decisiv. Cu cât sunt mai multe utilaje implicate, care trebuie coordonate eficient, cu atât este mai rentabilă automatizarea acestora, pentru a le putea exploata la maximum de potențial. Contează, de asemenea, dacă procesele desfășurate implică unul sau mai multe echipamente.
Dezvoltarea softului care să înglobeze întreaga aplicație și să coordoneze echipamentele printr-o interfață comună reprezintă un cost fix, efectuat o singură dată. În funcție de dimensiunea flotei, valoarea distribuirii acestui cost per echipament este mai mare sau mai mică.
Tehnologie performantă
Pentru operarea automată a echipamentele este necesară conectarea computerului de bord al acestora la o interfață software, menită să coordoneze toate procesele. Apoi, pe fiecare echipament în parte sunt instalați senzorii necesari realizării poziționării acestuia în interiorul depozitului și sisteme de scanare.
Toate echipamentele Still cu ghidaj automat (AGV) sunt prevăzute cu sistem de scanare 360O în jurul acestora, pentru ca în momentul în care apare orice fel de obstacol utilajul să încetinească sau chiar să oprească. Se asigură astfel operarea în condiții de deplină siguranță. Nu lipsesc sisteme clasice de detectare a greutății încărcăturii, a înclinării catargului sau a stabilității echipamentului, pe lângă sistemele laser și scanerele utilizate la navigație și la identificarea obstacolelor.
Foarte importantă este flexibilitatea sistemelor, grație tehnologiei DIY („do it yourself”), astfel încât, în funcție de schimbarea condițiilor de operare, managerul depozitului poate adapta programele de lucru și specificul operațiunilor. Esențial este și sistemul de navigație SLAM (simultaneous localization and maping), care analizează în detaliu spațiul dinamic din jurul echipamentului. Acesta din urmă trebuie să fie foarte performant, să aibă capacitatea de a înregistra o multitudine de parametri (care se pot schimba), transmiși de la toate AGV-urile din flotă, iar procesarea sarcinilor de lucru să se facă rapid (de preferat în timp real), pentru maximum de eficiență.
Nu în ultimul rând, modularitatea produselor și ponderea mare a componentelor comune între diferite modele permit productivitate crescută, disponibilitate mare a pieselor de schimb și costuri de exploatare reduse.
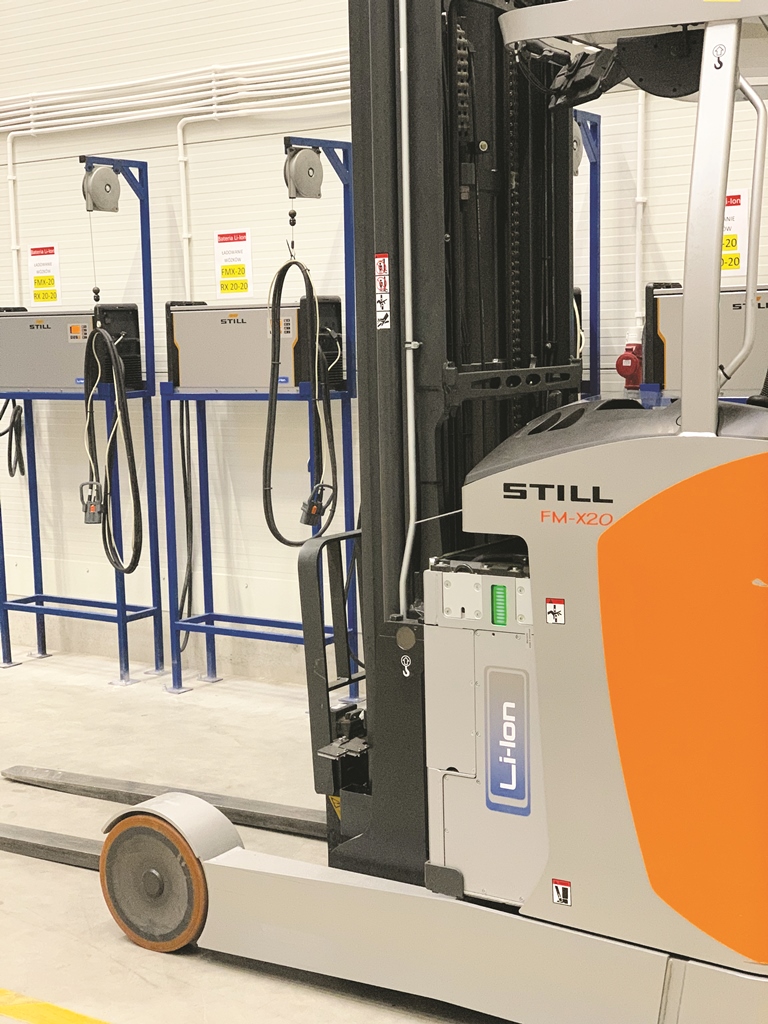
Care sunt costurile implementării sistemelor automatizate
O piedică actuală în automatizarea flotelor de echipamente o reprezintă costul de achiziție, deoarece mulți clienți nu țin seama și de costul total de operare pe întreaga durată de viață a utilajelor și de perioada de timp în care se poate amortiza diferența de bani plătită inițial.
Prețul AGV-urilor nu diferă foarte mult de la un producător la altul. Pallet-stacker-ele sau lift-stacker-ele automatizate, de exemplu, costă 60.000-70.000 de euro/unitate. Cum capacitatea de lucru este de 12-15 transporturi pe oră, pentru o aplicație ce presupune manipularea a 40 de paleți într-o oră sunt necesare trei utilaje. Prețul de achiziție al acestora – potrivit reprezentanților Still – se ridică la circa 200.000 de euro plus costul software-ului, care, în funcție de complexitate, poate ajunge până la 3.000 de euro. Este foarte ușor de calculat, prin urmare, amortizarea investiției, raportat la operațiunile și încasările fiecărei companii.
Reach-truck-urile automate au o tehnologie mai complexă: ridică mărfuri având între 1 și 2,5 t la înălțimi de până la 10 m. În cazul lor, în funcție de performanța dorită, prețul poate varia de la 110.000 la 150.000 de euro.
Cele mai complexe echipamente automate sunt VNA-urile. Acestea acoperă înălțimi de operare de până la 15 m, iar prețul poate ajunge de la 160.000 la 200.000 de euro. În cazul tuturor utilajelor automate încărcarea bateriilor se face autonom, fără a fi necesară intervenția umană. Sistemul de management al bateriilor este astfel programat încât alimentarea să se facă la momente oportune, fără a încetini procesele de lucru.
Amortizarea investiției se poate face – în funcție de aplicație – în 1-4 ani, iar echipamentele pot avea o durată de viață de până la 15 ani, dacă sunt întreținute corespunzător. De altfel, nici nu se recomandă automatizarea echipamentelor existente (reconversia unui utilaj second-hand convențional, chiar și relativ nou), deoarece este mai eficientă utilizarea unui echipament construit de la început pentru automatizare, plus că este de dorit exploatarea acestuia pentru o durată de timp cât mai lungă.
Este adevărat că vorbim de mulți bani, mai ales în această perioadă dificilă, de pandemie, recunosc specialiștii Still. Tocmai de aceea, soluțiile de leasing operațional/închiriere pe termen lung pot fi luate în considerare ca variante alternative. Se recomandă închirierea pachetului complet – utilaje, sisteme software, pachet de service și eventual conveioare.
Nu trebuie omise beneficiile suplimentare, care nu țin de investiția efectivă. Chiar și în țările unde costul cu forța de muncă este mai redus, criza de personal, lipsa angajaților calificați sau problemele de disponibilitate (de sărbători, pe timp de noapte etc.), de exemplu, pot fi rezolvate prin implementarea unor sisteme automatizate. În același timp, automatizarea elimină riscul accidentelor în depozit și, implicit, al costurilor directe și adiacente care rezultă de aici.
Consultanța și expertiza sunt esențiale
Pentru a avea succes în trecerea de la sistemul de operare manual la cel automat trebuie ales un partener cu experiență, care poate planifica în amănunt toate detaliile. Și aici, evident, consultanța și expertiza sunt esențiale.
Automatizarea trebuie făcută treptat și se recomandă începerea cu câteva procese simple, pentru ca abia ulterior să se extindă și la operațiunile mai complexe. Perioada totală de implementare – care include analizarea proiectului, producerea utilajelor necesare și instalarea propriu-zisă – va dura aproximativ un an, timp în care se menține contact permanent cu consultantul, pentru ajustarea și îmbunătățirea proceselor, acolo unde este cazul. Iar ulterior, după instalarea întregului sistem, locul consultantului va fi luat de responsabilul de service, care va superviza funcționarea echipamentelor și a soluției în sine.
Cel mai important, fiecare companie trebuie să analizeze care este nivelul optim de automatizare a proceselor, în funcție de aplicație, și apoi să vadă cum se pot integra noile sisteme în infrastructura existentă. Cu siguranță, la final, grație implementării de sisteme automatizate, se obține optimizarea sistematică a proceselor intralogistice.