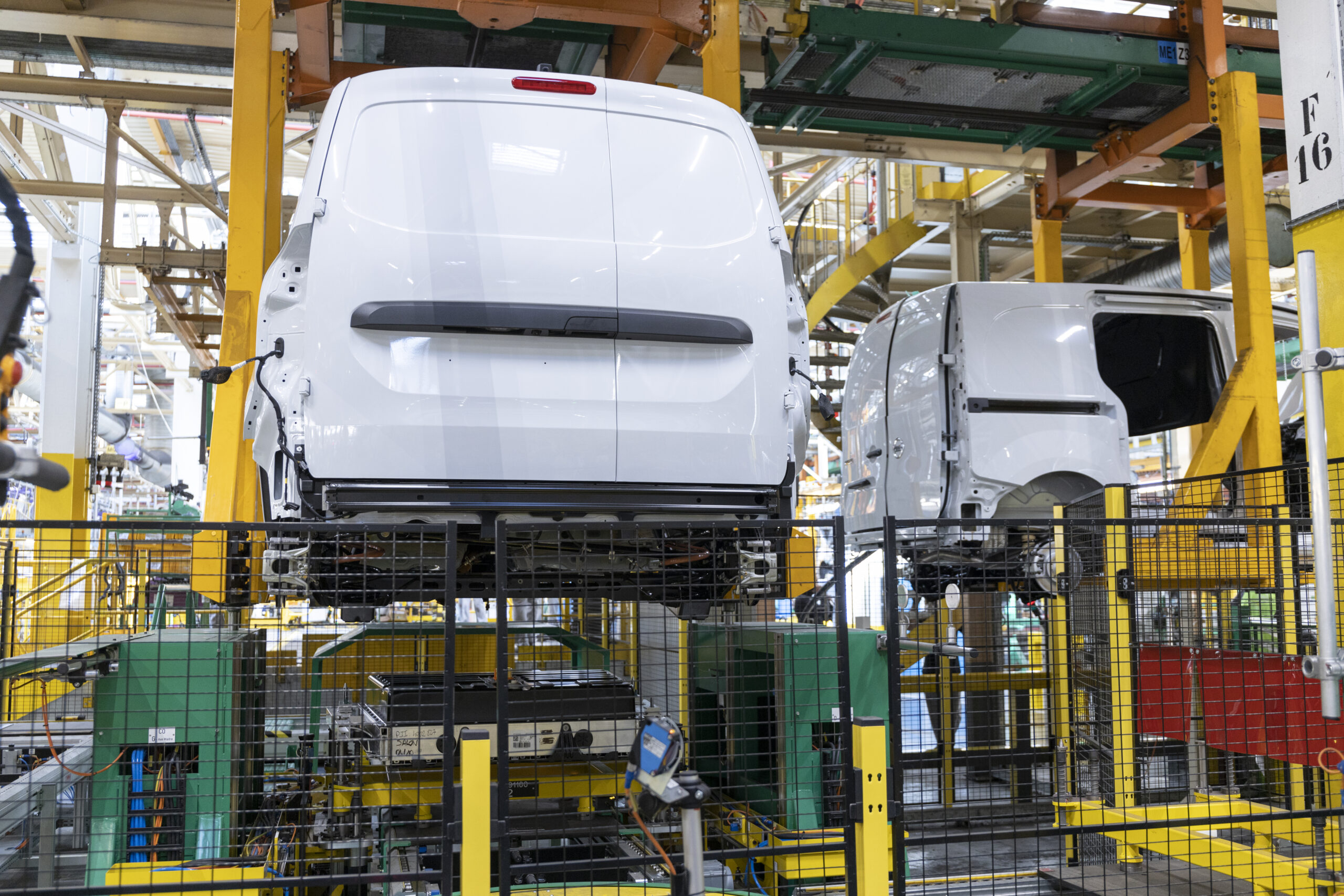
Un Renault Kangoo pe minut! Cu această cifră impresionantă, nici nu e de mirare că aproape 4 milioane de utilitare ușoare cu numele cangurului australian au fost produse la Maubeuge începând din 1997, odată cu prima generație. Am aflat mai multe despre cum este realizată utilitară, dar și despre viziunea Renault asupra mobilității electrice într-o vizită de fabrică pe care am efectuat-o recent. În numărul de Decembrie al revistei Tranzit veți putea citi un amplu reportaj despre această fabrică.
Pe aceeași linie de producție din Franța se produce și noul Nissan Townstar, dar și noul Mercedes-Bezn Citan. Pentru a reînnoii gamă astfel încât să poată găzdui toate versiunile mărcilor, inclusiv modelele electrice, Renault a investit la Maubeuge peste 450 de milioane de euro în modernizare, tehnologizare și creșterea capacității, dar și pentru instruirea angajaților.
Pentru a face loc celor mai noi modele ale celor trei mărci, fabrica și-a transformat atelierele de producție, îmbunătățind în același timp ergonomia și calitatea fiecărei stații de lucru. La noul Kangoo, peste 5.200 de puncte de sudură asigură o rigiditate structurală și un comportament de condus mult îmbunătățite, comparativ cu cele peste 4.000 de puncte la Kangoo de generația a doua. Între plafon și șasiu se sudează cu laser, deoarece este mai bine decât cu punctele de sudură, mai spune oficialul Renault. „În medie se fac 10 verificări pe oră cu sistemul de ultrasunet, care detectează un semnal și poate spune unde punctul de sudură nu este conform“, a explicat un oficial al companiei.
Pentru că se lucrează în paralel cele două generații de Kangoo (a doua și a treia), roboții portocalii alternează cu cei vopsiți în galben, aceștia din urmă fiind responsabili de carosarea noii generații Kangoo, pe când portocalii execută vechiul model. Mai mult de 800 de astfel de roboți galbeni a instalat Renault aici pentru noua generație Kangoo Van. „Avem o clădire satelit, dedicată logisticii, iar când vom întrerupe fabricarea actualul Kangoo, vom desființa clădirea pentru a mări spațiul de și a aduce toate componentele la interior“, mai spune acesta.
Pentru a produce cele peste 100 de variante diferite de caroserie, în acest atelier lucrează 400 de angajați în două schimburi. Manipularea pieselor între diferite zone ale fabricii, nu doar în această secțiune, este realizată cu ajutorul AGV-urilor (n.r. – vehicule ghidate automat) care nu doar îmbunătățesc eficiența și fac procesul de încărcare pe bandă mai rapid, dar cresc și siguranța, pentru că se opresc dacă întâlnesc un corp uman la o distanță prea mică. De menționat că tot aici, fiecărei caroserii i se atribuie și numărul de șasiu atunci când comanda intră în sistem, iar acel număr va fi folosit pe tot parcursul procesului de fabricație pentru a identifica mașina și componentele care o alcătuiesc. Înainte de a fi trimisă la vopsit, caroseria este verificată încă o dată de către o persoană care se asigură că totul este în perfectă stare.
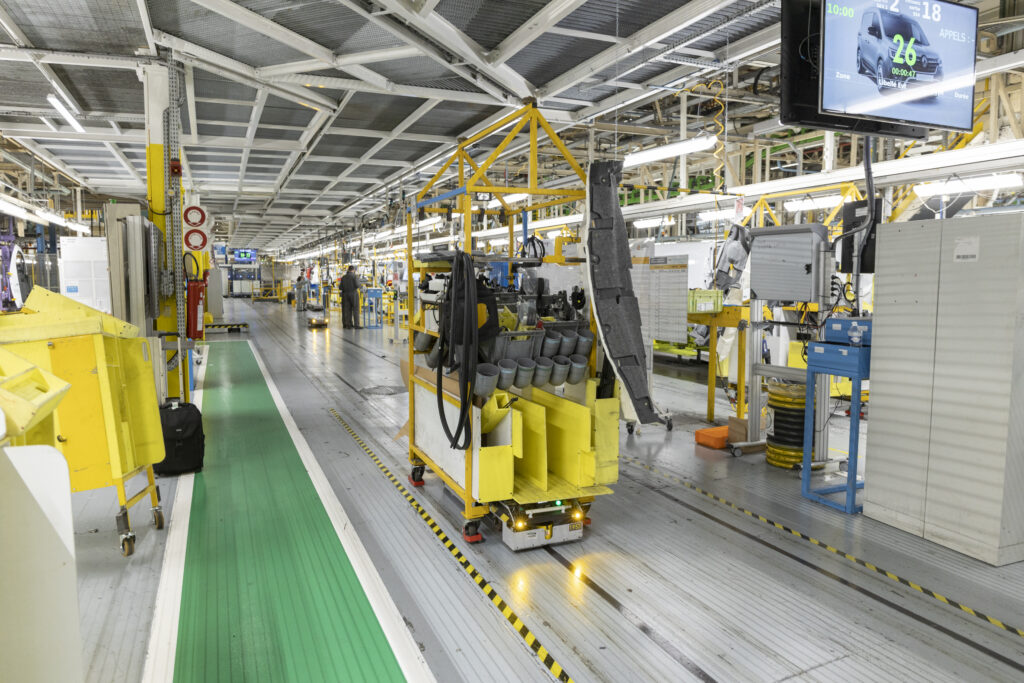
Digitalizarea și automatizarea permit un grad mare de diversitate
Liniile de producție și instalațiile au necesitat, de asemenea, măsuri de adaptare pentru a încorpora direct versiunile electrice de Kangoo, Townstar și Citan. Sunt 10 secțiuni de asamblare și 250 de stații de lucru. Un număr impresionant de oameni lucrează și aici, circa 850 de angajați în două schimburi. Dacă pe partea stângă am văzut ușile cum erau asamblate, pe partea dreaptă AGV-urile aduceau cutii cu părți componente ale mașinii – cabluri, țevi, furtunuri, manșete etc., iar operatorii le luau și începeau să le monteze. Am aflat ulterior că se numeau kit-uri și fiecare astfel de kit conținea 10 cutii diferite pentru fiecare vehicul. AGV-urile mergeau în paralel cu conveiorul, iar operatorul pur și simplu monta piesa pe bandă, apoi lua altă piesă din kit și tot așa. În total, aproximativ 2.000 de piese pentru fiecare vehicul.
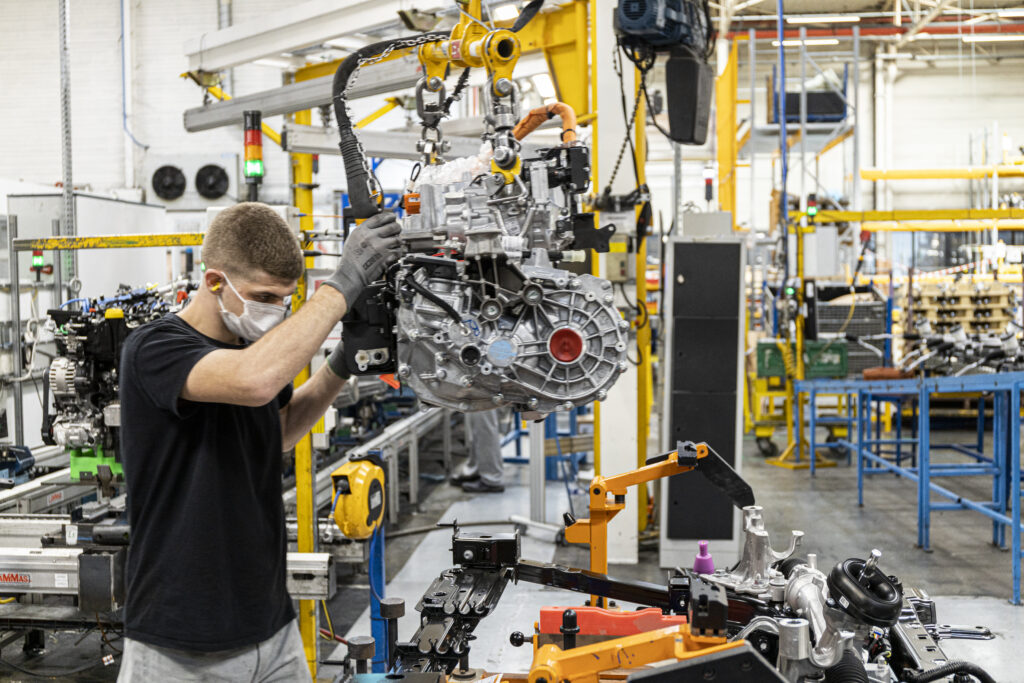
La final din linia de producție a fabricii Maubeuge ies 53 de mașini pe oră, adică aproape un Kangoo Van la fiecare minut, însă înainte de a lua drumul clienților, fiecare vehicul trece pe la bancul de probă unde, printre altele, se verifică etanșeitatea prin „testul dușului“. Controlul static este realizat de 20 de persoane, iar apoi se merge la pista de teste pentru controlul dinamic.