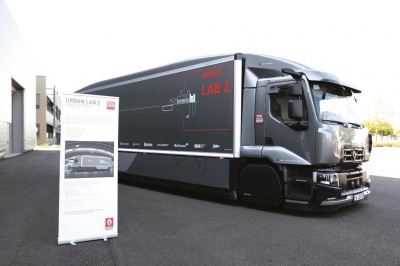
In cadrul unui eveniment special dedicat membrilor juriului „International Truck of the Year“, ce a avut loc la sediul central al Renault Trucks din Lyon, specialistii companiei ne-au aratat cum imbina aceasta tehnologia de maine cu produsele de azi. Am asistat astfel la trei workshop-uri despre fabricatia aditiva AM (Additive Manufacturing) sau printarea 3D, asa cum este cunoscuta, cel mai nou proiect al companiei in termeni de eficienta – vehiculul Urban Lab 2 Trucks – si Realitatea Augmentata, ce va deveni o operatiune standard in cadrul controlului de calitate al motoarelor Renault Trucks.
Cunoscuta si sub alte denumiri, precum fabricatie aditiva, prototipare rapida sau fabricare rapida, printarea 3D a fost introdusa in cadrul Renault Trucks in urma cu circa trei ani, in cadrul unui proiect intern prin care s-a urmarit crearea unui motor DTI 5 Euro 6 step C, de patru cilindri, proiectat exclusiv prin utilizarea acestei tehnologii. „Sunt mai multe procese prin care poti obtine parti de motor prin imprimarea 3D, noi ne-am focusat pe SLM (Selective Laser Melting), acolo unde vedem cele mai mari posibilitati de dezvoltare a tehnologiei pe viitor“, ne-a explicat specialistul Renault Trucks. Astfel, desi motorul a fost proiectat virtual, culbutorii si capacele arborelui cu came au fost fabricate prin tehnologia imprimarii metalice 3D, fiind testate cu succes in cadrul simulatoarelor, timp de 600 de ore in cadrul unui motor real Euro 6. Scopul acestui proiect a fost acela de a vedea impactul pozitiv oferit de printarea 3D asupra greutatii si marimii unui motor. Astfel, specialistii Renault Trucks au facut echipa cu cei din cadrul a doua companii si a doua universitati specializate in aceasta tehnologie (in total 15 oameni), iar la finalul proiectului, dupa noua luni, au redus greutatea motorului cu 120 kg si peste 200 de piese, de la 525 kg si 841 de piese. „Testele pe care le-am realizat demonstreaza durabilitatea componentelor realizate prin printarea 3D, nu este doar cosmetica“, au spus oficialii companiei franceze. „Tintele noastre erau de minus 30% in termeni de greutate si 40% mai putine componente ale motorului“, a mai detaliat ghidul nostru.
Pana sa ajunga la rezultatul final, specialistii in fabricatia aditiva au generat peste 100 de idei pentru diferite propulsoare, pentru ca mai apoi sa defineasca o arhitectura a motorului. La final au avut de ales intre a realiza un motor nou, total diferit fata de ce exista astazi, si a pastra aceeasi arhitectura, pentru a putea compara beneficiile aduse de noua tehnologie. A fost aleasa cea de-a doua varianta si au fost pastrate 35 de idei, multe concept review-uri si studii de design pentru a produce partile. In noua luni tot motorul a fost testat cu piese realizate prin tehnologia imprimarii 3D din materiale precum otel inoxidabil, titan, aluminiu sau inconel (un aliaj din nichel, ce contine crom si fier, rezistent la temperaturi inalte si coroziune). Momentan, singurul inconvenient pe care il are aceasta tehnologie este timpul. De exemplu, pentru a produce 12 piese sunt necesare 100 de ore, ceea ce inseamna ca masinaria lucreaza non-stop timp de patru zile. Specialistii Renault Trucks au explicat faptul ca tehnologia inca este la inceput si pe masura ce va avansa acest dezavantaj va fi redus treptat. Este si motivul pentru care piesele realizate prin imprimarea 3D nu pot fi produse in volume mari, ci doar 100 pe an.
Urban Lab 2, laboratorul mobil ce promite o eficienta de pana la 13%
Renault Trucks lucreaza de mai multa vreme la proiectul Urban Lab 2, care vizeaza reducerea consumului de carburant in mediul urban si regional. Proiectul este finantat de guvernul francez si este dezvoltat impreuna cu sase parteneri: Valeo (tehnologia micro hibrid), Lamberet (caroserie), Michelin (anvelope cu rezistenta redusa la rulare), BeNomad (sisteme de navigatie) si doua institutii de invatamant superior – INSA Lyon (LamCoS) si IFSTTAR (LICIT).
Vehiculul – un camion D Wide E6 (19 t) echipat cu tot felul de tehnologii menite sa scada consumul de motorina cu pana la 13% – nu este un vehicul demo, „ambitia fiind sa fim gata cu proiectul pana la jumatatea lunii decembrie. Testam fiecare tehnologie in privinta reducerii consumului de combustibil, apoi testam cum functioneaza toate aceste tehnologii impreuna.“ Scopul Urban Lab 2 este de a oferi inovatii accesibile pana in 2020, concentrandu-se asupra a patru zone cheie: aerodinamica, lant cinematic, conectivitate si anvelope. „Tehnologiile pe care le folosim, credem noi, ar putea fi solutii pe termen mediu sau scurt. Vorbim de 2020, iar tinta este sa vedem daca aceste tehnologii sunt profitabile, ce economie de carburant aduc ele. Cand ne referim la tehnologie as spune ca, desi sunt patru piloni pe care ne focusam, vorbim de fapt de cinci tehnologii.“
1. Eco-ruta
Alaturi de inginerii de la Renault Trucks, specialistii de la BeNomad au proiectat un GPS care il ghideaza pe sofer pe cel mai economic traseu din punct de vedere al carburantului. Practic, „Eco Routing“ este un mix intre experienta celor doua companii, o noua caracteristica in sistemul de navigatie al camionului prin care soferul poate economisi carburant. Acesta introduce adresele si orele la care trebuie sa fie la fiecare dintre ele, iar sistemul calculeaza eco-ruta. La final insa, soferul este liber sa aleaga ce ruta doreste.
2. Semafoare inteligente
Ca si sistemul de navigatie bazat pe ruta cea mai economica, Urban Lab 2 este conectat la infrastructura pentru a optimiza consumul cu ajutorul semafoarelor aflate pe culoarea verde. Practic, cand vehiculul se apropie de un semafor, computerul de bord primeste informatii din partea acestuia si stie daca e cazul ca soferul sa franeze sau sa accelereze, in functie de conditiile de trafic si de legislatia in vigoare. Inginerii de la IFSTTAR (LICIT) au ajutat Renault Trucks sa integreze efectul acestei solutii asupra consumului de carburant. Tehnologia este insa departe de a fi folosita la scara larga, cel putin in orasele din estul Europei, care inca nu au infrastructura pregatita.
3. Aerodinamica
De ce ar reduce cineva coeficientul de rezistenta a aerului la un vehicul de distributie care se deplaseaza prin oras? Pentru a afla raspunsul, inginerii Renault Trucks, au analizat mai multe flote ale clientilor si au constatat ca viteza medie a camioanelor pe distanta peri-urbana (metropolitana) a fost de peste 50 km/h. Iar daca tii cont de o asemenea cifra trebuie sa tii cont si de aerodinamica. Pentru a reduce coeficientul, inginerii au lucrat pentru a optimiza fluxul de aer pe toata lungimea vehiculului. Parteneriatul a fost realizat cu Lamberet, iar unitatea aleasa a fost una frigorifica. „Am ales acest tip de caroserie pentru ca este cea mai complexa pe care o puteam schimba, deoarece agregatul frigorific este deasupra cabinei, iar daca optimizarea aerodinamica este realizata din acest punct, atunci putem extinde solutia la furgoane obisnuite“, a mai explicat Project Managerul. Agregatul frigorific a fost coborat sub remorca, in zona ampatamentului. In locul acestuia a fost pozitionat un deflector, asigurandu-se fluiditatea cu caroseria. Lamberet a proiectat o caroserie functionala, certificata de o institutie abilitata din Franta. Lateralele Urban Lab 2 au fost prevazute cu deflectoare din material textil acoperit cu PVC, o premiera pentru companie.
4. Anvelopele
Michelin a facut din nou echipa cu Renault Trucks pentru a dezvolta anvelope destinate economisirii energiei pentru vehiculele de distributie. Pentru a reduce rezistenta la rulare fara a compromite siguranta, longevitatea sau aderenta, Michelin a dezvoltat o gama larga de tehnologii, cum ar fi Infini-Coil, care ofera rezistenta si siguranta pneurilor.
In sfarsit, Renault Trucks si partenerii sai si-au stabilit tinta ambitioasa de a reduce consumul de combustibil cu 13% in comparatie cu un Renault Trucks D WIDE echivalent. Vehiculul a fost testat pentru prima data intr-un circuit inchis in noiembrie 2016 si pe drumuri in Bordeaux din februarie 2017. Rezultatele vor fi prezentate la sfarsitul proiectului, programate pentru 2018.
5. Sistemul Stop&Start si tehnologia micro-hibrid
Pentru a reduce consumul de combustibil, Urban Lab 2 beneficiaza de un propulsor inovativ multumita combinatiei dintre tehnologia micro-hibrida si sistemul Stop&Start, dezvoltate in parteneriat cu Valeo. Sistemul taie alimentarea atunci cand vehiculul se opreste, de exemplu la un semafor, reducand astfel consumul de combustibil. In plus, sistemul micro-hibrid recupereaza energia generata in timpul rularii libere, prin intermediul unui motor electric reversibil de mare putere (48 V). Energia recuperata astfel poate fi utilizata pentru a actiona diversele componente electrice aflate in interiorul cabinei sau pentru a reduce puterea mecanica necesara motorului termic. Renault Trucks a colaborat cu Lyon INSA pentru a reduce frecarea in partea frontala a motorului, optimizand astfel eficienta generala a sistemului micro-hibrid.
Realitatea augmentata, o… realitate in cadrul Renault Trucks
Al treilea workshop a fost si cel mai interactiv dintre toate. Am avut ocazia sa testam realitatea augmentata prin intermediul unor ochelari Microsoft, al caror software este dezvoltat de specialistii Renault pentru a se potrivi nevoilor companiei. Incepand din 2018, Renault Trucks va efectua controlul calitatii motoarelor prin intermediul realitatii augmentate. Proiectul este implementat de o echipa de 25 de oameni, iar prototipul va fi lansat pana la finalul acestui an. De ce investeste compania energie in aceasta tehnologie? „In primul rand vrem sa crestem calitatea controlului pentru a ne asigura ca nu avem probleme cu motoarele care ajung la clientii nostri. Acum avem un mix de solutii digitale si hartie. Vrem ca aceasta ultima parte sa o inlocuim. Cel de-al doilea motiv este legat de celelalte companii din industrie care se misca in aceasta directie, Tesla, Schneider Electric si Bosch. Nu in ultimul rand, daca ne uitam la cifre, «realitatea augmentata» va fi o piata de 60 de miliarde de dolari pana in 2022. Jucatorii mari se dezvolta cu pasi rapizi in aceasta directie, cumpara companii cu milioane de dolari. Industria va folosi din ce in ce mai mult realitatea augmentata in asamblare, in reparatii, in controlul de calitate, trainingul oferit operatorilor sau in operatiunile logistice din depozit“, a punctat trainerul Renault Trucks. Am avut ocazia sa ne transformam chiar noi in operatori de control al calitatii pentru cateva minute. Procesul este destul de simplu, chiar daca nu ai urmat cursuri in acest sens. Elementele pe care trebuie sa le verifici iti apar pe lentila dreapta, acolo unde exista o schita a motorului aflat in fata ta, iar piesa ce trebuie verificata este evidentiata printr-o culoare portocalie. Dupa ce ai verificat-o fizic, pe motorul real, tot ce trebuie sa faci este sa dai check virtual cu ajutorul degetelor, iar sistemul te trece automat la urmatoarea operatiune pe care o ai de facut. In total, pentru un singur motor, operatorii Renault Trucks au de efectuat 40 de astfel de operatiuni.