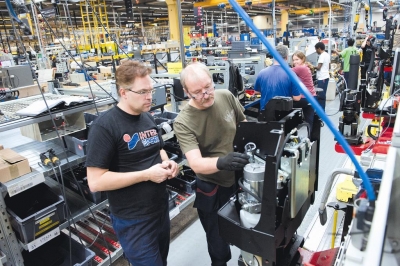
Toyota Material Handling Europe (TMHE) a mostenit la Mjölby, in Suedia, o istorie de aproape 60 de ani in producerea de echipamente de depozitare. Grupul japonez a pastrat aici experienta furnizorilor si calitatea fortei de munca, implementand in acelasi timp modul sistematizat de productie japoneza. Fosta fabrica BT Products se bucura acum nu doar de investitii in tehnologie de ultima ora, dar si de un plus de productivitate, in conditiile in care fiecare angajat este direct responsabilizat pentru calitatea productiei.
Fabrica Toyota Material Handling din Mjölby (Suedia) a fost infiintata de BT Products AB in 1946 si a inceput activitatea propriu-zisa cinci ani mai tarziu. Primul model produs a fost transpaleta manuala BT.
Odata cu preluarea BT de catre TMH, in 2000, a urmat o perioada de cativa ani in care grupul japonez s-a familiarizat cu procesele de productie de la Mjölby, dupa care s-a trecut la implementarea sistemului de productie Toyota (TPS), pentru eficientizarea activitatii in conditiile mentinerii calitatii operatiunilor.
Astfel, s-a ajuns de la constructia pe posturi de lucru la sistemul de asamblare pe linii de productie, in care echipamentele sunt transferate intr-un flux continuu de la o statie la alta. Rezultatele implementarii TPS sunt evidente si pot fi masurate, gratie unor tehnici de supervizare a productiei si controlului riguros al calitatii. In plus, fiecare angajat este implicat in procesul de control, iar daca descopera de-a lungul fluxului de productie o eroare poate anunta acest lucru, echipamentul fiind retras pentru remediere. Fiecare zi de munca incepe cu o scurta sedinta in fiecare departament de productie, pentru a identifica eventualele deficiente. Totul este documentat, iar problemele care apar sunt urmarite pana la sursa, pentru a fi eliminate.
Rezultatul este „kaizen“, ceea ce inseamna „imbunatatire continua“.
„Suntem in derularea procesului de continua imbunatatire a calitatii produselor subcontractorilor nostri si lucram in stransa colaborare cu ei pentru a ne asigura de acest lucru. Un alt termen-cheie pe care il avem in vedere in permanenta este «muda», care se traduce prin «risipa», de materiale sau de timp. Iar pe termen lung obiectivul este de a elimina de tot aceasta risipa din operatiunile noastre“, a explicat Anders Claesson, director executiv BT Products AB.
Implementarea noilor standarde de productie reduce riscul erorilor si creeaza o atmosfera mai relaxata in randul angajatilor, care isi pot planifica munca mai bine.
La Mjölby se proiecteaza si se produc echipamente de interior cu comanda electrica si manuala, care sunt distribuite in toata lumea, cu precadere in Europa. Se primesc si comenzi speciale, cu diferite configuratii sau optiuni cerute de clienti.
Fabrica din Mjölby acopera acum o suprafata de 76.000 m2, in conditiile in care la inaugurare avea numai 28.000 m2.
Principalele procese tehnologice sunt productia de foi de metal si componente sudate, vopsitoria, asamblarea produselor standard si a celor cu design special. Acestea reprezinta aproximativ 30% din valoarea finala a echipamentelor. Restul componentelor utilizate in productie vin de la furnizori independenti. Chiar si otelul vine din mai multe surse, in special din Suedia, dar si din Germania sau Finlanda. De regula, componentele livrate pentru asamblare vin direct in forma si la calitatea dorita, fara a fi impuse alte tratamente speciale.
Productie structurata pe familii de echipamente
La Mjölby se lucreaza pe patru linii principale de asamblare, pe sistemul „primul intrat, primul iesit“, care se aplica si in cazul pieselor de schimb aflate pe stoc. In dreptul fiecarui post sunt aduse componentele necesare, astfel incat productia sa se deruleze intr-un flux continuu. Din momentul in care un echipament intra in productie, el este monitorizat in permanenta, existand un panel care arata etapa din productie la care acesta se afla.
Distributia pe liniile de productie se face in functie de familia din care face parte fiecare echipament: transpalete manuale, transpalete electrice automate (order-pickere), transpalete electrice cu catarg (stackere) si electrostivuitoare cu catarg retractabil (reach-truck). Separat, exista o zona unde se asambleaza toate celelalte modele care se produc in volume mai mici, inclusiv VNA-uri. Pe linia de asamblare, in functie de complexitatea echipamentelor, sunt intre sapte si zece posturi de lucru.
Capacitatea fabricii este de 1.100 de echipamente pe saptamana. Timpul de livrare pentru produsele realizate in volume mari este intre patru si opt saptamani, iar pentru cele mai putin solicitate si pentru configuratiile speciale poate ajunge la 10 saptamani. De la fabrica din Mjölby se distribuie produse in toata lumea, inclusiv spre China.
Toate etapele de productie sunt standardizate, conform TPS, astfel incat sa se obtina o eficienta cat mai mare a proceselor derulate. Fiecare operatiune trebuie desfasurata intr-un anumit timp, iar la fiecare post de lucru exista documentatie privind executia si poze relevante in acest sens. Dupa finalizarea operatiunii pe fiecare etapa in parte se face verificarea calitatii, in acest sens fiind urmarit un opis cu aspecte ce trebuie avute in vedere, iar la final se face controlul calitatii intregului produs.
Angajatii se rotesc intre diferite posturi de lucru cel putin o data pe zi, pentru a nu interveni rutina in operatiunile executate. Orice problema constatata pe linia de asamblare trebuie remediata in maximum 24 de ore.
Perioada de productie difera pe tipuri de echipamente, dar, chiar si pentru modelele mai mari, nu depaseste o zi: sudura se face in 30 de minute, iar fiecare etapa dureaza circa cinci minute.
Investitie de 12 milioane de euro la vopsitorie
Sasiurile intra in productie dupa un tipic si prin respectarea etapelor de sudura se asigura eliminarea defectelor in productie. Aici procesele au fost reorganizate, miza principala fiind cresterea productivitatii. Inainte, etapele de sudura se faceau in diferite zone ale halei, pierzandu-se timp cu transportul sasiului dintr-un loc in altul.
Dupa sudura, sasiurile, dar si celelalte componente, merg la vopsitorie. Fiecare este incarcata pe o linie automatizata, pentru un transport aerian facil si economic in camera de vopsire. Inainte de vopsirea propriu-zisa, elementele care trebuie vopsite sunt pre-tratate, spalate si racite.
Recent, la Mjölby a fost inaugurata o noua instalatie pentru vopsit, cu una dintre cele mai moderne tehnologii din Suedia, ce aduce beneficii importante legate de protectia mediului, reciclarea de materiale si recuperarea energiei. Capacitatea de vopsire este de 80.000 de echipamente pe an, care, evident, nu este atinsa la acest moment, dar lasa loc de extindere si dezvoltare pe viitor. Trei cabine moderne „gazduiesc“ robotii care deruleaza toate operatiunile. In doua cabine se vopseste in negru, iar in alta in portocaliu. Daca se doresc culori speciale se pot introduce intr-una dintre cabine.
Investitia in linia de vopsitorie este cea mai mare facuta pana acum la nivelul fabricii, respectiv de 12 milioane de euro. Timpii de vopsire s-au redus semnificativ, iar productivitatea a fost sporita. Angajatii nu au acces decat la incarcarea componentelor pe liniile automatizate care le transporta pe tot procesul de vopsire.
Pentru ca operatiunile de productie sa fie cat mai ecologice, la Mjölby functioneaza si o instalatie de tratare a apelor reziduale. Apa tratata este refolosita, facandu-se astfel o economie substantiala. Si in hala de vopsitorie se calculeaza in permanenta nivelul de poluare, care trebuie mentinut cat mai scazut. Faptul ca toate operatiunile se deruleaza automatizat implica un consum minim de vopsea si pierderile sunt astfel limitate.
Inainte de criza economica, la Mjölby se lucra in doua schimburi. Odata cu reducerea volumelor de productie s-a trecut la unul singur, cel de seara fiind oricum mai costisitor. In plus, au fost operate si restructurari, care nu au putut fi evitate.
Din cei 1.300 de angajati de la Mjölby, 400 au studii superioare.