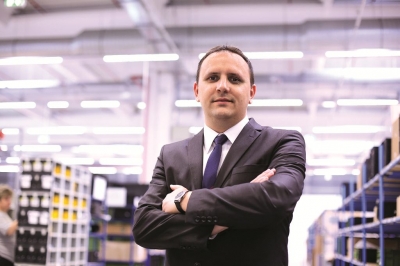
Construita in 2006, fabrica Hella din Timisoara a devenit curand binecunoscuta si apreciata de majoritatea producatorilor de masini importanti din Europa. Cateva milioane de componente sunt fabricate aici in fiecare an, cele mai multe fiind exportate catre producatorii de masini de top. Avand in vedere nivelul ridicat de calitate cerut in acest domeniu, fiecare angajat nou beneficiaza de o pregatire speciala, indiferent de functia din cadrul companiei. Furnizorul international se straduieste sa depaseasca industria auto in urmatorii ani si sa tina cont de tendintele pe piata auto europeana, cum ar fi electrificarea, conducerea autonoma, conectivitatea si individualizarea.
Hella a venit in Romania in 2005 si detine in prezent trei unitati de productie in Romania, la Timisoara, Arad si Lugoj, precum si trei centre de proiectare si dezvoltare la Timisoara si Craiova. Fabricile de la Timisoara si Arad produc sisteme electronice de diferite tipuri, in timp ce fabrica din Lugoj – sisteme de iluminat si optice.
Prima entitate din Romania a fost fabrica de la Timisoara, construita in 2006, care a beneficiat de la bun inceput de personal calificat cu experienta, datorita faptului ca in aceasta zona a existat timp de cativa ani o fabrica de electrocasnice unde o parte din oamenii care au venit ulterior la Hella fusesera instruiti. Totusi, aici au ajuns la un nivel de calitate mult mai ridicat decat cel cerut in cazul produselor de consum. „Daca aparatele electrocasnice pot fi inlocuite cu usurinta, cerintele din domeniul auto sunt mult mai mari, deoarece o componenta defecta poate pune in pericol viata oamenilor atunci cand masina este pe drum. Prin urmare, din 2005 ne dezvoltam experienta in domeniul auto, capacitatea de a testa, verifica si aproba acest tip de produse“, a explicat Alin Cuc, directorul adjunct al fabricii Hella Timisoara.
Hella Romania are in prezent peste 4.300 de angajati directi. Cei din domeniile industriale asociate beneficiaza de instruire. „Industria auto s-a dezvoltat extrem de mult si, din moment ce nu exista un know-how local, este necesar sa investesti in fiecare angajat, indiferent de functia lui in cadrul companiei“, a spus Alin Tapirdea, directorul general Hella din Romania.
Mai multe milioane de piese sunt fabricate in fiecare an
In Romania, Hella produce cateva milioane de piese pe an. Exista patru familii de produse, care includ 11 grupuri, fiecare cu 40 de tipuri de produse. „De exemplu, avem trei familii de actuatoare din fiecare familie, doua familii de sisteme de administrare a bateriilor, unitate de gestionare a celulelor (CMU) si unitate de gestionare a bateriilor (BMU), impartite in mai multe tipologii“, a spus Alin Cuc.
De asemenea, aici se produc pedale si un sistem electronic care controleaza pompa de injectie si nu numai. Pentru un client extern se produce modulul Body Control (calculatorul auto). „Fabricam mai mult de 60.000 de unitati pe saptamana. Sistemul este format din doua parti, una care controleaza partea din spate a masinii, cealalta partea din fata, mai exact farurile, stergatoarele de parbriz etc.“
Pentru un alt client important fabrica produce si un sistem de gestionare a bateriei pentru masinile electrice. „Cred ca masinile electrice sunt viitorul. Electrificarea vehiculelor continua sa creasca in forta; numarul vehicululelor cel putin partial electrice va continua cu siguranta sa creasca.“
Zona dedicata servodirectiei electronice
Fabrica Hella Timisoara se intinde pe o suprafata de 17.200 m2, care include o zona pentru receptia materiilor prime, una pentru productie si o alta dedicata produselor finite. Depozitul de materii prime se intinde pe o suprafata de 2.500 m2 si este impartit in trei zone: una de receptie, unde marfa este descarcata din camion si receptionata, si doua laterale pentru depozitare, echipate cu rafturi obisnuite si rafturi in care sunt pastrate rolele sunt pentru componentele electronice.
Depozitul pentru produse finite acopera 2.000 m2, iar aici sunt stocati aproximativ 6.000 de paleti si sunt pregatite livrari urgente, pentru care nu exista timp sa fie transferate partenerului logistic al companiei. Tot aici este stocata si o gama de produse care are nevoie de securitate avansata, mai precis computerele care controleaza partea de deschidere/inchidere a masinii cu cheie, adica partea care se potriveste cu cheia masinii, pe care clientul o doreste pastrata intr-un sistem securizat pentru a evita furturile de coduri care pot programa cheile automobilelor.
Initial, suprafata pentru produsele finite era de 2.500 m2, dar 500 m2 din aceasta zona erau dedicate unei noi activitati, Electronic Power Steering (EPS), unde sunt fabricate sisteme electronice de servodirectie. „Directia mecanica sau servodirectia nu mai sunt utilizate in productie, deoarece folosesc mai multe piese, in timp ce directia electronica foloseste piese numai atunci cand este actionat volanul, ceea ce contribuie la reducerea consumului de combustibil si energie si ofera o precizie mai buna a directiei. Cu alte cuvinte, acesta poate intari sau slabi foarte usor cuplul motorului care ajuta la rotirea volanului.“
In ultimii ani, s-au facut o multime de investitii in acest domeniu pentru a-l adapta la noua activitate. De exemplu, podeaua trebuie sa fie ESD (descarcator electrostatic), deoarece piesele pot fi deteriorate din cauza descarcarilor electrostatice. Desi angajatii folosesc echipamente ESD, descarcarea electrostatica nu poate fi realizata fara acest tip de podea. O alta solutie este aceea ca angajatii poarta o bratara care se conecteaza la statia de lucru, iar descarcarea electrostatica se face prin legarea la pamant a statiei.
Particule de praf, masurate cu atentie
La cererea clientilor, zona ESP a trebuit sa indeplineasca si conditia de curatenie tehnica, adica eliminarea particulelor de praf, deoarece acestea pot crea un scurtcircuit. „O componenta are ace metalice care asigura contactul pe placa. Daca o particula de praf mai mare decat distanta dintre doi pini ajunge aici, exista riscul de scurtcircuit. In cazul unui scurtcircuit exista riscul ca o functie a acestui microcontroler, care actioneaza ca un microcomputer, sa nu se activeze, iar daca acesta este un produs foarte important in siguranta de functionare a vehiculului, poate provoca un accident. Astfel, particulele de praf nu trebuie sa fie mai mari decat jumatate din distanta dintre doi pini, adica putin mai putin de jumatate de milimetru, pentru a evita orice posibila scurtcircuitare. Elig Map este utilizat pentru a efectua masuratori in acest sens. O banda adeziva este plasata pe diferite zone ale partii verificate, apoi capcanele de praf sunt colectate si dimensiunea si densitatea particulelor de praf sunt masurate la microscop.“
Presiunea inversa este utilizata pentru a impiedica particulele de praf sa intre in acea zona. Cu alte cuvinte, din camera in care nivelul de praf trebuie sa fie foarte scazut se impinge mai multa presiune decat se trage aer. Astfel, orice lucru care vine din exterior ca o particula atunci cand o usa este deschisa, de exemplu, tinde sa fie impins afara. Cele mai multe particule provin din exterior, apoi oamenii pot aduce si particule de praf, motiv pentru care au pantofi de rezerva cu care nu au voie sa iasa afara, un halat de protectie si o sapca, deoarece praful poate veni si din par. „Aceasta tehnica isi are originile in industria farmaceutica, unde este cel mai inalt nivel de curatenie tehnica. In aceasta industrie, chiar si colturile camerei sunt rotunjite pentru o mai buna curatare, deoarece majoritatea prafului este colectat din astfel de zone.“
Directorul adjunct al fabricii Hella Timisoara a explicat ca industria auto evolueaza puternic spre curatenie tehnica, deoarece piesele utilizate in acest domeniu sunt din ce in ce mai mici. „In trecut, existau releele, care aveau dimensiuni mari, deci nu exista un risc ridicat daca erau produse in conditii de praf. In zilele noastre exista microcontrolerele, care, fiind mult mai mici, sunt influentate de absolut tot ce exista in mediu. La final, le sigilam pentru a preveni contactul cu apa sau praful. Dar pana atunci trebuie sa evitam contactul cu anumite particule de praf. Acesta este motivul pentru care am creat toate conditiile pentru aceasta zona. Celelalte produse pe care le fabricam au un nivel de securitate care nu pune in pericol viata soferului.“
In prima faza, produsele sunt ambalate in pachete ESD deoarece, pentru a evita praful, nu sunt aduse cutii de carton in fabrica. Ambalajul este fabricat in cutii returnabile care apartin cel mai adesea clientilor. Le primesc, le folosesc si apoi le trimit inapoi la Hella. Compania le trimite partenerului logistic care le spala in cadrul unei instalatii specializate si le reintroduce in circuit.
Coroziunea poate deteriora piesele
Un departament din companie planifica zonele de productie. Prima zona se numeste SMT (dispozitive montate pe suprafata), unde sunt montate componentele. De exemplu, pentru BMS (sistemul de gestionare a bateriei), primul pas este SMT, ceea ce inseamna a pune componentele mici pe placa. Se monteaza pe o linie separata, apoi se testeaza si se taie placa. „SMT, produce o cantitate mai mare de placi, le luam, le punem pe linii si le introducem in procesele specifice fiecarei operatii. O masina introduce pinii, apoi se efectueaza testarea si se aplica un lac pentru a preveni coroziunea. Coroziunea este un fenomen de oxidare in staniu, care este un metal. Daca rugina intra intre ace, poate deveni particule de contact si placa poate fi deteriorata. Un test este efectuat pentru a verifica functionalitatea, adica este simulata o realitate teoretica a produsului. Dupa aceea, produsul este ambalat si trimis clientilor.“
Inovatii Hella apreciate de marii producatori
Hella pune un accent deosebit pe inovatie, astfel incat componentele sale sa fie apreciate de marii producatori. Un produs Hella 100% dezvoltat in centrul Hella Craiova este Comfort Control Module, un modul care controleaza intreaga zona de deschidere si inchidere automata a portbagajului.
Mai mult, exista linii automate de productie proiectate de expertii Hella, dar fabricate de furnizori. Astfel, s-au gandit sa asambleze un produs cu o interventie umana minima. „Avem o linie cu o iesire a unui produs in 18 secunde, cu interventia unei singure persoane, care furnizeaza linia cu materiale, elimina produsele finite ce sunt deja ambalate, rezolva cateva blocaje si scrie raportul. Nicio alta interventie nu este efectuata de aceasta persoana.“
Aproximativ 70.000 de actuatoare de turbocompresoare sunt fabricate aici in fiecare saptamana, aceasta fiind o alta inovatie Hella care a castigat numerosi clienti. Cea mai mare parte a productiei este exportata.
Schimb de experienta
De asemenea, compania are partea Best Practice, ceea ce inseamna ca entitatile Hella impartasesc cu colegii lor solutiile pe care le gasesc. De exemplu, pe linia SMT exista un cuptor care topeste in cele din urma pasta, dar temperaturile care trebuie aplicate sunt diferite. „Astfel, este simplu sa incalziti cuptorul la o temperatura mai mare, dar este dificil sa-l raciti atunci cand este nevoie de o temperatura mai scazuta. Si colegii de aici au inventat o solutie pe baza de azot, folosita pentru o racire mai rapida a cuptorului. ”
Automatizarea a crescut treptat
Gradul de automatizare a fabricii a crescut treptat. In 2014, conducerea companiei a gandit o schema conform careia, daca volumele anuale sunt mai mari de 800.000 de piese dintr-un anumit reper – indiferent de complexitate – atunci merita investitia in automatizare. In caz contrar, utilizarea insuficienta a robotilor face automatizarea nerentabila. In 2019, limita a fost reconsiderata la aproximativ 500.000 de repere identice pe an, „pentru ca oamenii au devenit mai scumpi si mai greu de gasit decat in 2014. Dar, in timp ce un angajat este platit in functie de ceea ce produce, pentru automatizare, ca sa faci o investitie, e nevoie de toti banii odata si, daca exista volabilitate pe piata, riscul e mare”.
Achizitiile se fac la nivel global
Materiile prime din tari precum China sunt comandate la nivel de containere, in timp ce cele provenite de la partenerii autohtoni, cum ar fi o fabrica de materiale plastice situata in apropierea fabricii Hella, sunt comandate zilnic. „Daca furnizorul este situat in apropiere, poate alimenta direct linia de productie, dar nu am ajuns inca la acest nivel, care este de obicei utilizat de producatorii de masini.“
Produsele din China sosesc cu vaporul in Hamburg, Rotterdam sau Gdansk. „Avem contracte globale pentru mai multe fabrici din Europa, precum cele din Germania sau Lituania. Astfel, din port, produsele sunt grupate si expediate la fabrica pe cale rutiera.“
In cele mai multe cazuri, Hella angajeaza transportatori pentru a aduce materia prima in fabrica, dar exista si situatii cand este mai convenabil ca furnizorii sa aduca produsele. Transportul produselor finite este organizat de catre clienti, deoarece reusesc sa-si eficientizeze transporturile.
Fluxul de numerar depinde de o planificare corecta
La planificarea productiei contribuie in primul rand informatiile primite de la clienti prin comenzile introduse in sistem, care, mai departe, trimite comenzile pentru materiile prime. Comenzile lunare sunt impartite pe saptamani, apoi pe zile.
Daca in lunile de vara se iau in considerare comenzile fixe in proportie de 98%, din septembrie se foloseste un instrument din SAP numit APO (Advance Planning Operations). Este nevoie de cererile de anul trecut si anul acesta de la MDB (Market Data Base) si se face o previziune pentru urmatorii doi ani. „Cu toate acestea, acest APO opereaza pe o piata fara fluctuatii mari. Si acum am observat ca incetinirea economica incepe sa se simta. Ar trebui sa putem influenta predictia unui astfel de instrument folosind anumiti parametri, deoarece, in caz contrar, exista riscul de a bloca sume importante de bani in materiale“, a spus Alin Cuc.
Viitorul apartine masinilor electrice
Alin Tapirdea, director general Hella Romania a explicat ca proiectele companiei iau in considerare tendintele de pe piata auto europeana, care sunt: electrificare, conducere autonoma, conectivitate si individualizare. „Prin individualizare, vreau sa spun ca fiecare producator incearca sa iasa in evidenta individual printr-un aspect legat de proiectare sau de anumite functii specifice ale masinii sale. In urma acestor tipuri de individualizare, vorbim despre noile tendinte in domeniul auto, inclusiv BMS si servodirectia electronica. In zona Aplicatiilor Speciale, unde sunt incluse sisteme de iluminat, exista o crestere a cererii de componente electrice si electronice pentru orice vehicul, cu exceptia autoutilitarelor. Mai precis, producatorii de camioane, autoutilitare sau chiar utilaje agricole incearca sa-si puna amprenta asupra sistemelor de iluminat pentru a iesi in evidenta. Daca ne uitam la lampile din spate din camioane sau din remorci, putem vedea ca fiecare are ceva unic. Unii au inceput sa lumineze logo-ul producatorului. Aceste tendinte sunt evidentiate de noi procese si produse care vor fi industrializate in Romania pentru prima data la nivel global.“
Aceste schimbari nu presupun modificari masive la nivelul fabricii, potrivit lui Alin Tapirdea, care a explicat ca vor veni echipamente de noua generatie si vor fi facute investitii asociate. „Tehnologiile vor fi diferite, dar nu este o diferenta majora, care implica un nou set-up al fabricii. De fapt, interiorul fabricii a suferit intotdeauna schimbari.“ Alte planuri se concentreaza pe dotarea fabricilor cu tehnologiile necesare pentru componentele vehiculelor electrice si, in aceasta privinta, sunt luate in considerare investitii importante, deoarece sunt necesare alte echipamente decat cele detinute in prezent. De exemplu, BMU functioneaza cu un voltaj mare, astfel incat este necesar un test de inalta tensiune, pentru a testa izolatia galvanica, iar curentul electric sa nu ajunga la utilizator. Exista, de asemenea, elemente care pot fi adaptate la noua tehnologie, cum ar fi SMT, dispozitivul care plaseaza componentele pe placa.
La cererea companiei-mama de a reduce consumul de combustibil cu 2% in fiecare an, la fabrica Hella becurile obisnuite au fost inlocuite cu LED-uri. „Tehnologia LED aduce numeroase avantaje si pentru masini, precum reducerea consumului de energie si imbunatatirea iluminarii. Mai mult, au o durata de viata mai lunga decat becurile conventionale, ajungand chiar la 4.000 de ore.“