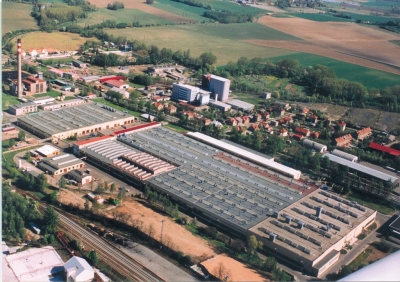
Fabrica Irisbus Iveco de la Vysoke Myto este un centru de productie cu traditie in Republica Ceha, avand o istorie de mai bine de 100 de ani. Dar numai micul muzeu din interiorul incintei mai aminteste de primele vehicule construite aici la sfarsitul secolului al 19-lea, pentru ca acum totul functioneaza dupa cele mai inalte standarde tehnologice
si de calitate. La Vysoke Myto se realizeaza toata productia Irisbus Iveco de autobuze intercity si low-entry, precum si o parte din productia Citelis, pentru transportul public. Si vorbim de un proces complet, de la taierea si prelucrarea foilor de tabla, constructia sasiului si a structurii de rezistenta si pana la asamblare si efectuarea testelor finale.
Activitatea la Vysoke Myto este impartita in patru zone operationale: o hala de sudura si operatiuni de prim-montaj, o zona speciala pentru tratament anti-coroziune si vopsitorie, o hala de asamblare si o a patra unitate, aflata intr-o locatie separata, in acelasi oras.
Procesele primare de productie constau in prelucrarea foilor de metal, cu grosimi intre 1 si 3 mm, care sunt taiate cu ajutorul a cinci masini cu laser (tot ce depaseste aceasta dimensiune se achizitioneaza de la furnizori). Utilajele sunt dispuse pe laterale, lasand zona din mijloc pentru depozitarea foilor de metal, de toate dimensiunile. Masinile cu laser dispun de sisteme speciale de protectie a angajatilor impotriva accidentelor de munca. De asemenea, toate au o evidenta computerizata a operatiunilor si fiecare muncitor poate verifica pe computer cum trebuie sa arate in final lucrarea. In plus, exista si trei utilaje folosite la taierea si prelucrarea componentelor de dimensiuni mici.
In aceeasi hala se prelucreaza elementele lungi de caroserie, inclusiv panourile laterale. Acestea, dupa ce sunt finalizate, merg mai departe la sectiunea de sudura, unde sunt atasate scheletului vehiculelor folosindu-se sudura in puncte. Tot in hala de sudura este amenajata si o zona speciala unde se taie tuburi. Toate elementele de caroserie au mici perforatii care asigura ca procesul ulterior de cataforeza sa se desfasoare corect, iar vopseaua sa patrunda pe interiorul structurilor metalice.
Elementele de sasiu care trebuie sudate sunt fixate pe utilaje speciale, care se pot roti la 180o, pentru a facilita efectuarea tuturor operatiunilor corect si in timp cat mai scurt. Dupa finalizarea sasiului, pe acesta sunt sudate celelalte elemente de structura si apoi panourile laterale. Numarul operatiunilor fiind mare, ele sunt impartite pe posturi de lucru, respectandu-se o anumita succesiune. Munca este astfel usurata si se poate lucra la mai multe vehicule in acelasi timp.
Componentele sunt transportate la diferitele posturi de lucru cu ajutorul macaralelor industriale. Cele mai importante elemente ale structurii, cu rol in siguranta pasiva, sunt sudate cu ajutorul a cinci roboti industriali. Este vorba de operatiuni de mare precizie, care, in acelasi timp, economisesc mult timp, iar pentru a spori eficienta se doreste achizitionarea unui numar suplimentar de roboti. Totusi, acestia nu pot fi folositi decat pentru elementele standardizate, comune pentru toate vehiculele. Scheletul, odata finalizat, este trimis mai departe pentru a fi tratat anti-coroziune prin scufundarea intr-o baie cataforetica.
Dupa incheierea procesului de sudura, scheletul vehiculului trece printr-un proces de control. In urma cu doi ani, in fabrica de la Vysoke Myto s-a instalat un sistem nou de ventilatie, pentru a se mentine o calitate cat mai buna a aerului.
La ora actuala se produc 12 autobuze pe zi, in doua schimburi, cu exceptia sectiunii de prelucrare a foilor de tabla, unde se lucreaza in trei schimburi pe zi in fiecare zi a saptamanii, datorita volumelor mari de produse care trebuie prelucrate.
Tratament anti-coroziune prin cataforeza
In hala de vopsitorie sunt parcurse doua etape. Prima este procesul de tratare anti-coroziune a scheletului vehiculului prin procesul de cataforeza, iar a doua este vopsirea propriu-zisa. Intr-o prima faza, scheletul este spalat foarte bine si degresat, dupa care este scufundat intr-o baie cu vopsea, care este atrasa de acesta printr-un flux de curent electric. Timpul petrecut in baia de vopsea este de 20 de minute, atat pentru structura vehiculului, cat si pentru un cos metalic unde se gasesc alte componente ce urmeaza sa fie montate ulterior (usi, bara de protectie etc.).
Dupa 20 de minute scheletul este ridicat din vopsea cu ajutorul unei macarale. Se asteapta o scurta perioada de timp pentru scurgerea vopselei in exces, dupa care structura se usuca in cuptor, la o temperatura de 200oC. De fapt este nevoie de minimum 180oC temperatura pe toata suprafata, dar, pentru mai multa siguranta, se merge pe 200oC.
Urmatoarea etapa este cea de racire a scheletului tratat. Intreg ciclul este automat, iar instalatia de cataforeza este construita pe doua niveluri, pentru a putea fi realizata ridicarea si scufundarea in baia de vopsea.
Vopseaua din baia de cataforeza trebuie tot timpul amestecata, pentru ca altfel se usuca foarte repede. Iar daca sunt probleme cu alimentarea cu curent electric exista generatoare care intra imediat in functiune, pentru a asigura continuitatea procesului.
Aproximativ 30 kg de vopsea se ataseaza de fiecare vehicul la procesul de cataforeza (in functie de lungimea acestuia). Atelierul de vopsitorie functioneaza in doua schimburi.
Linia de cataforeza a fost inaugurata in urma cu 10 ani si prima data cand a fost umpluta baia cu vopsea a costat trei milioane de coroane cehesti (peste 100.000 de euro). Tocmai de aceea este importanta intretinerea vopselei.
Structura si elementele care sunt inca detasate de aceasta primesc dupa cataforeza un al doilea strat de vopsea protector si abia dupa aceea se aplica stratul final, cel de exterior. Totul se realizeaza cu ajutorul robotilor, iar apoi se fac retusuri manuale, acolo unde robotii nu au reusit sa ajunga foarte bine. Uscarea celui de-al doilea strat de vopsea se face la o temperatura de 120oC, in timp ce vopseaua de exterior se usuca la 80oC.
Dupa ce se incheie vopsirea urmeaza un alt proces de control, cu ajutorul unor lumini speciale. In afara de calitatea procesului de vopsire se verifica si grosimea stratului.
Un sigur autobuz poate avea mai multe culori sau mai multe tonuri din aceeasi culoare.
Linie de asamblare in forma de „S“
Dupa vopsire si uscare, structura si celelalte componente sunt trimise la linia de asamblare.
Aceasta este organizata in forma literei S, iar vehiculele trec de la un post de lucru la altul pe niste carucioare pneumatice, care au si roti, si sine. Primele doua etape sunt dedicate asamblarii unor elemente de interior, dar si a cablurilor electrice si a tuburilor transversale de la nivelul podelei, pentru apa, aer conditionat, care nu mai pot fi montate dupa ce se asambleaza podeaua.
In etapa a patra se izoleaza compartimentul motorului, pentru a-l proteja de zgomot si caldura. Desi componentele se gasesc la fiecare post de lucru in parte, se folosesc si carucioare speciale pentru transportarea celor grele. Carucioarele au mai multe variante de ajustare, astfel incat componentele sa poata fi aduse pana in interiorul vehiculelor.
Urmeaza montarea celorlalte componente de interior, a bordului, dar si a geamurilor, care sunt lipite si apoi asigurate cu banda adeziva. Aceasta din urma va ramane pe geamuri pana cand vehiculul paraseste linia de asamblare.
Pe ultima parte a acesteia autobuzul este ridicat pentru a se monta sistemul pneumatic, motorul si transmisia. Urmeaza instalatia de racire, sistemul de evacuare a gazelor de esapament, axele fata si spate, rezervorul de combustibil si rotile. Montarea tuturor elementelor importante se face cu ajutorul unor masini speciale cu memorie, care inregistreaza toti parametrii de montaj, pastrati la istoricul masinii. Acestia pot fi comunicati si proprietarului. Componentele foarte grele sunt si aici manevrate cu echipamente speciale pneumatice.
Urmeaza efectuarea tuturor conexiunilor, ajustarea pozitiei usilor si montarea celorlalte componente electronice.
La final, vehiculul se alimenteaza cu motorina, apa, lubrifianti si se porneste pentru prima data motorul, care va functiona timp de 10 minute. Cu aceasta ocazie se elimina tot aerul din componente. In final se face controlul calitatii pentru sectiunea de asamblare. Fiecare autobuz are carte tehnica privind specificatiile tehnice si configuratia interioara.
Autobuzele pleaca din fabrica pe roti, pe un traseu special de teste, pentru a se verifica sistemul de franare, accelerare, comportamentul pe diferite tipuri de drum etc. Dupa aceasta testare initiala urmeaza un al doilea test, pe o distanta de 50 km.
Dupa aceea vehiculul se spala si se face testul de apa. Cu jeturi de apa din podea, plafon si lateral, timp de 20 de minute, se verifica daca exista scurgeri la interior. Operatiunea este efectuata de angajati Irisbus Iveco aflati in interiorul vehiculului.
Ultimele elemente de design exterior se adauga acum, intr-un atelier special de vopsitorie pentru astfel de operatiuni.
12 autobuze pe zi
Capacitatea maxima la Vysoke Myto este de 16-17 autobuze pe zi, dar in prezent se construiesc doar 12. Aici se produc Crossway intercity si LE, Arway, Evadys H si Citelis (ultimele doua modele au intrat in fabricatie de putin timp, fiind construite si la fabricile de la Annonais – Franta – si Vale Ufita – Italia). Toate modelele sunt disponibile in diferite lungimi, de la 10,6 la 15 m.
Fabrica de la Vysoke Myto se intinde pe o suprafata de 225.828 m2, dintre care 61.329 m2 sunt construiti. Din 2000 pana in 2010 au fost facute investitii de 71 de milioane de euro. Anul trecut au fost construite 1.390 Crossway, 562 Crossway LE, 192 Arway si 33 Citelis, iar pentru 2011 se estimeaza in total 2.056 de Crossway, 713 Crossway LE, 246 Arway, 129 Citelis si 72 de Evadys H.