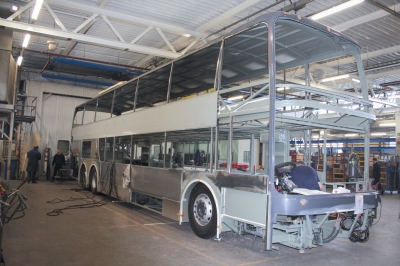
VDL Bus&Coach este in plin proces de reorganizare a productiei in toate cele sapte fabrici din Belgia si Olanda, obiectivul fiind de a crea o platforma comuna atat in ceea ce priveste constructia de autobuze si autocare, cat si pentru celelalte servicii conexe, in special unificarea diviziei de piese de schimb. Chiar daca unele schimbari au fost privite cu neincredere, inclusiv de catre clienti cu traditie in operarea autocarelor Bova sau Jonckheere, VDL Bus&Coach si-a schimbat complet imaginea si logo-ul, iar in scurt timp intreg demersul – curajos de altfel – de reorganizare din temelii a productiei va fi incheiat. La fabrica VDL Valekenswaard, fosta Bova, productia se desfasoara conform programului, chiar daca multe operatiuni sunt in curs de relocare si trec printr-o faza tranzitorie. Dar ce a fost mai greu a trecut, iar finalul se prefigureaza sa fie un succes.
Crearea unei imagini unitare a VDL Bus&Coach a insemnat si redenumirea tuturor fabricilor din grup. Astfel, fosta fabrica Berkhof se numeste acum VDL Bus Heerenveen, unde se produc o parte din autobuzele urbane, fosta Jonckheere este VDL Bus Roeselare, fabrica Bova se numeste acum VDL Valekenswaard, iar peste drum, in acelasi oras, este VDL Bus Modules. In Helmond se produc autobuzele articulate Philleas, in Venlo este fabrica VDL Bus Venlo, pentru gama midi/mini, iar la Eindhoven este fabrica de sasiuri VDL Bus Chassis.
Fabricile VDL Bus Modules (VBM) si VDL Bus Valekenswaard (VBV) au intrat intr-un proces complex de modernizare si automatizare a unei sectiuni importante din productie, in conditiile in care, pana la integrarea in grupul VDL, etapele de productie si structura erau traditionale.
Belgia si Olanda sunt printre cele mai scumpe locuri de productie din Europa, iar costurile cu forta de munca sunt mult mai mari in comparatie cu cele ale constructorilor care si-au deschis fabrici in Europa de Est sau chiar in afara continentului. In momentul in care s-a decis modernizarea fabricilor, unul dintre principalele obiective a fost cresterea capacitatii de productie, in conditiile mentinerii calitatii vehiculelor. De asemenea, optimizarea costurilor auxiliare productiei este esentiala – vorbim de acele costuri „nevazute“.
Productia noului Futura este acum impartita intre cele doua fabrici. VBM produce toate componentele de pre-fabricatie prin operatiuni de sudura, indoire, taiere etc. si modulele ce urmeaza sa fie asamblate, iar la VBV se realizeaza asamblarea propriu-zisa, inclusiv vopsirea si controlul final (momentan, procesul de verificare a executiei se face acum inca in ambele fabrici, pentru un plus de operativitate). In prezent, aici se mai asambleaza autobuzul Axial si autocarul supraetajat Synergy, aflate pe final de productie. Anul acesta vor fi realizate 40 de Axial si 55 de Synergy. Primul dintre ele va iesi din productie inainte de 2013, in timp ce Synergy va ramane, dar va fi reproiectat, astfel incat sa se incadreze in familia noului Futura din punct de vedere al designului exterior. Nici Futura clasic nu va mai ajunge la Euro 6, iar productia Magiq a fost deja oprita din vara lui 2010.
In urmatorii doi ani va continua distribuirea proceselor intre cele doua fabrici si va incepe robotizarea. Primul robot va veni la sfarsitul acestui an, iar in termen de doi ani vor fi amenajate noua cabine pentru sudura, cu roboti. In momentul de fata ruleaza doua proiecte pilot de optimizare a productiei. Primul este la vopsire, iar celalalt la constructia modulului fata al caroseriei. De asemenea, la nivel de personal, se doreste cresterea gradului de specializare, in vederea sporirii eficientei. De altfel, statisticile arata ca pe viitor s-ar putea sa apara o criza a fortei de munca, motiv pentru care angajatii trebuie sa vina cu placere la locul de munca si sunt incurajati sa aiba rezultate foarte bune.
Constructia noului Futura
Futura a fost un succes inca din faza de proiect, astfel ca inainte de a avea primele autocare demo au fost comandate 200 de unitati in timp de trei luni. „Mandria operatorilor de a detine un autocar VDL este un lucru pe care trebuie sa il castigam in fata clientilor nostri. Acordarea distinctiilor Bus of the Year 2011 pentru Citea si Coach of the Year 2012 pentru Futura ne face sa fim increzatori in faptul ca suntem pe drumul cel bun cu schimbarile radicale pe care le facem la nivelul gamei de produse. Tocmai de aceea am si utilizat aceste titluri in promovarea celor doua modele la nivel european”, a explicat Rémi Henkemans, director general VDL Bus&Coach.
Futura are o structura integrala, care imbina partile de rezistenta cu elementele usoare, menite sa reduca greutatea proprie a vehiculului. Toate subansamblurile se produc separat, pe linia finala de productie facandu-se doar imbinarea acestora. Se obtine astfel o viteza mai mare pe linia de asamblare. Un alt avantaj este faptul ca productia modulara ofera mai multe oportunitati de control.
Elementele de structura sunt produse in fabrica VBM. Baza o constituie un schelet de otel 3Cr12, separat fiind realizate scheletele peretilor laterali. De altfel, procentul de otel inoxidabil in constructia scheletului este de 95%, iar in zona motorului, pentru a se obtine o rezistenta suplimentara, se foloseste fier. 80% din rezistenta la rasturnare este data de arcadele fata si spate din otel, iar restul vine de la peretii laterali.
Toate elementele sunt taiate cu laser, operatiunea fiind realizata cu sprayere cu gaz, pentru a preveni coroziunea. Dupa constructia asa-zisului sasiu se face vopsirea anti-coroziune, care ofera o garantie de 12 ani, iar apoi structura este transportata in hala de asamblare din VDL Bus Valekenswaard. Aici se pun laolalta toate componentele caroseriei, dupa care se monteaza toate tuburile necesare pentru cabluri si alte racorduri, motorul, cutia de viteze, radiatorul si intercooler-ul, axele fata, spate si portanta, se amenajeaza compartimentul de bagaje, se pun incalzitoarele, sistemele de franare si cele de aer. Avantajul este ca muncitorii au la dispozitie foarte mult spatiu pentru a putea asambla toate elementele.
Urmatorul pas este montarea si acoperirea podelei, montarea toaletei si a cusetei de dormit pre-asamblate si, apoi, a peretelui spate. Se asambleaza peretii laterali, apoi acoperisul (prin lipire) si scaunele (introduse prin partea din fata). Dupa ce se fac toate finisajele la interior se ataseaza sectiunea din fata, de asemenea, pre-asamblata. La final se adauga usile, trapele de la compartimentul de bagaje, rotile si scaunul ghidului, dupa care vehiculul trece printr-o verificare amanuntita.
Aproximativ 70% dintre componentele montate pe linia de asamblare sunt deja vopsite in culoarea finala a autocarului. Restul vopsirii se face la final. De asemenea, sunt cazuri cand operatorul solicita anumite combinatii de culori. Avand in vedere faptul ca pe linia de asamblare intra componente vopsite in varianta finala, se impune o acuratete foarte mare a operatiunilor.
Transportul intre cele doua fabrici, pe o distanta de 1,5 km, se face cu ajutorului unui camion cu remorca.
Linia de asamblare este in forma de „S“, Pe zona centrala se pregatesc modulele ce urmeaza a fi asamblate: partea din spate, peretii laterali (cu perdelele montate) si partea din fata. Plafonul este singurul care vine direct de la VBM gata de asamblare. Daca vopsirea elementelor de sasiu se face la VBM, cele de caroseriei sunt vopsite la VBV, in 18 cabine. La fiecare cinci ore si 45 de minute un autobuz iese de pe linia de fabricatie.
30 de unitati pe saptamana vor fi asamblate in momentul in care toate modificarile se vor fi facut, respectiv in 2013. Pe perioada verii s-au asamblat sase Futura in patru zile, plus alte patru unitati din modelele vechi, pentru ca volumul de munca este mai mic. Ziua in minus se compenseaza pe timp de iarna, cand comenzile sunt numeroase si se lucreaza cinci zile plus ore suplimentare. Iar atunci se executa 8-10 vehicule intr-o saptamana intreaga de munca.
2011 va fi inchis cu aproximativ 200 de autocare Futura noi, iar pentru anul viitor se estimeaza productia a 500 de unitati, din totalul de 1.600-1.800 de vehicule complete (fara sasiuri si fara gama midi).
VDL Parts coordoneaza toata activitatea pe piese
Schimbarile in cadrul VDL au impus adaptarea activitatii after-sales. In trecut, fiecare fabrica era responsabila cu productia de piese de schimb pentru vehiculele construite, iar un client putea primi chiar si trei livrari diferite si trei facturi. Acum este mult mai simplu, iar gestionarea stocurilor de piese de schimb si onorarea comenzilor primite de la toti furnizorii din teritoriu intr-un timp foarte scurt intra in sarcina VDL Parts. Centralizarea stocurilor de piese de schimb a inceput in 2004, iar termenul de finalizare a procesului a fost inceputul lui 2011. Un grup de lucru format din toti directorii after-sales de la toate fabricile VDL au avut sarcina de a se coordona si de a gasi o platforma comuna de lucru. In mai 2005 a fost elaborat programul VIP, cu rolul de a pune in comun informatiile despre stocurile de piese existente. In 2006 a fost infiintat VDL Parts, o companie noua care a reunit toate diviziile fabricilor VDL. Principala problema a reprezentat-o integrarea in acelasi program a reperelor pentru autobuze si a celor pentru autocare, mai ales ca fiecare dintre divizii avea modalitati proprii de identificare si contabilizare a stocurilor. In mai 2008 a fost implementat programul SAP, care a usurat mult activitatea. Tot in acel an a fost mutat depozitul central de piese de schimb la Veldhoven, un orasel in apropiere de Valekenswaard. A fost ocupata o suprafata mai mare, de 14.000 m2, iar obiectivul a fost dublarea cifrei de afaceri.
In martie 2009 a fost integrat si sistemul after-sales pentru autobuzul articulat Philleas, care este vandut in Belgia si Turcia.
Coordonarea este esentiala
O prioritate a reprezentat-o stabilirea unei platforme comune de identificare a pieselor de schimb si unificarea politicii tarifare si de discounturi. In acest sens, a fost creat un numar nou de identificare pentru toate reperele de pe stoc, din opt cifre. De asemenea, a fost creat un sistem tarifar VDL unic la nivel european, cu o noua politica de acordare a discount-urilor.
Comparand 2006 cu 2011, atunci erau 16.000 de repere, iar acum sunt 113.000. S-a inceput cu 215 furnizori, iar acum sunt peste 600. Totul poate fi gestionat foarte usor insa prin programul SAP, iar activitatea s-a dezvoltat, astfel incat numarul liniilor de comenzi a crescut de la 42.000 la 175.000.
Pe timp de criza, vanzarea de piese de schimb a scazut cu 3%, acest lucru datorandu-se diminuarii puternice a cererilor pe segmentul autocarelor. S-a reusit o usoara compensare pe exporturile catre alte continente, in special spre Africa de Sud. Pretul pieselor de schimb este intotdeauna orientat in functie de pretul pietei, chiar daca materiile prime se scumpesc.
Livrarile se fac direct catre reprezentantele VDL, cu exceptia conturilor mari, cum ar fi Veolia sau Arriva, care primesc comenzile direct.
La centrul de la Veldhoven se preiau si se executa toate comenzile de piese, astfel ca activitatea se desfasoara contra cronometru. Departamentul de achizitii si logistica este responsabil cu dinamica pieselor de schimb la nivelul depozitului. Se tine o legatura stransa cu reprezentantii tuturor familiilor de produse si se ofera toate componentele, cu exceptia celor pentru motoarele DAF, acestea servisandu-se in reteaua proprie. In fiecare luna vin pe stoc 500 de repere noi de piese de schimb.
Stocurile sunt controlate prin programul SAP, dar rolul important revine responsabililor cu aprovizionarea si vanzarea de piese, care fac estimari periodice, precum si dinamica recenta a pieselor. In sistem sunt nu mai putin de 50.000 de repere, in conditiile in care volumul de autobuze si autocare vandute nu este foarte mare. Problema este insa data de diversitate.
Departamentul operational se ocupa cu onorarea comenzilor in timp scurt, iar acestea vin prin surse diferite. 60% dintre comenzi sunt urgente, astfel ca livrarea se face peste noapte, inclusiv pentru destinatii din afara Olandei.
Activitatea la centrul de piese de schimb incepe la sapte dimineata si se incheie la sase seara. Cu toate ca se lucreaza inca manual pentru picuirea comenzii, s-a implementat si sistemul cu coduri de bare, care acum este in probe. In momentul in care ajung la depozit, piesele sunt pre-ambalate, astfel incat cand se pregatesc livrarile timpul necesar alcatuirii pachetelor sa fie cat mai scurt. Mai ales ca dupa-amiaza se aglomereaza comenzile.
In cadrul aceluiasi depozit functioneaza zone dedicate pentru inlocuirea pieselor aflate in garantie, dar si de inlocuire a celor vechi cu altele noi. Unele repere sunt in sistem de miscare rapida, care, de altfel, aduc si cel mai mic profit, dar pe fiecare categorii de piese exista si repere cu miscare lenta, care au o pozitionare speciala, pentru ca stau mult timp pe stoc.
Unele tipuri de piese, la care furnizorii merg pe cantitati minime, sunt pe suprastoc.
Odata ce un vehicul iese din productie, piesele trebuie sa se mai produca inca 10 ani. Sunt insa si contracte de furnizare pe perioade mai mari, de 12 sau 15 ani.
La depozitul de la Veldhoven sunt aduse si resturile ramase din productie la inchiderea unei serii de vehicule, iar acestea sunt pastrate ca piese de schimb. In 98% din cazuri se stocheaza si mulajele.