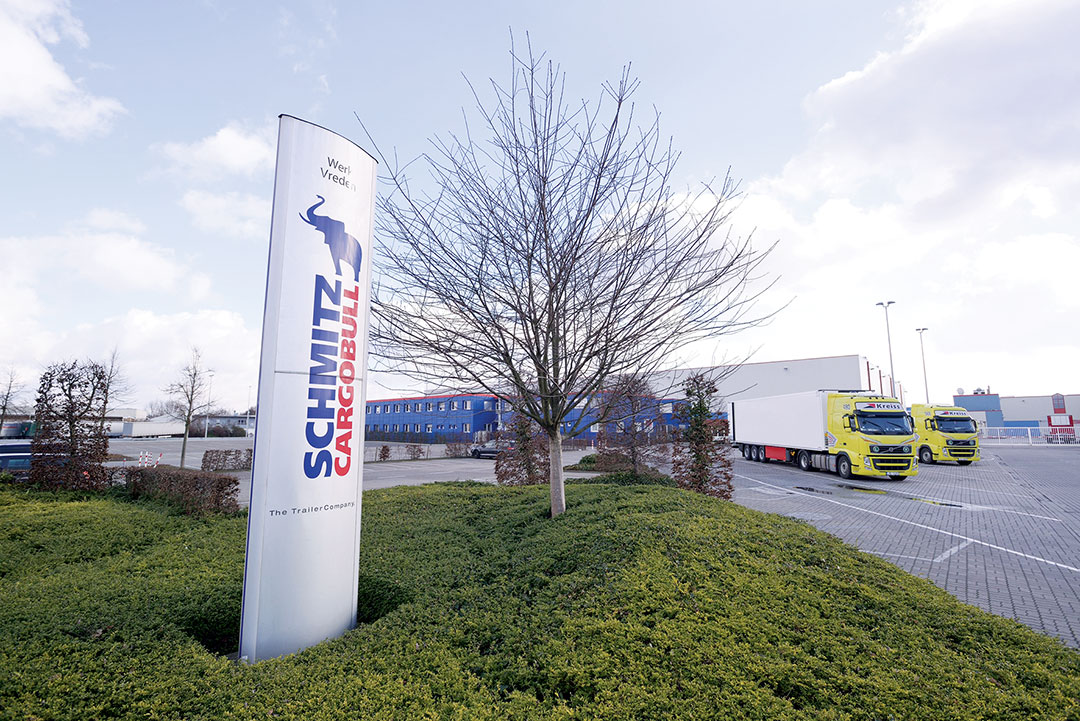
Cu ocazia evenimentului premergător IAA Hanovra pe care Schmitz Cargobull l-a organizat în iunie am vizitat fabrica din Vreden, premiată de multe ori pentru inovații și procese, unde lucrează circa 2.000 de angajați care produc semiremorci S. KOe Cool și S. KO Cool pentru temperatură controlată și semiremorci izoterme S. BO Express și S. BO Pace, precum și agregate frigorifice și panouri Ferroplast și Struktoplast. Capacitatea fabricii poate ajunge la 21.300 de unități/an, iar în prezent se investesc peste 65 de milioane de euro în extinderea acesteia și în creșterea competitivității, mai exact, în construirea unei fabrici digitale, automatizate, la standarde înalte de calitate, în care spațiul să fie folosit optim și care să se alăture fabricii actuale.
Schmitz este prezent pe piață din 1892, iar în Vreden din 1969. Dintre cele mai importante inovații pe care le-a propus de-a lungul timpului, aici se produc, din 1977, panourile Ferroplast, care garantează o izolare foarte bună a semiremorcilor pentru transport la temperatură controlată, din 2012 agregatele frigorifice S. CU, din 2022 semiremorcile frigorifice electrice S. KO2 Cool și din 2023 noile agregate frigorifice hibrid pentru piața din SUA. Alte momente memorabile sunt fabricarea, începând din 1982, a semiremorcilor frigorifice double deck, care dublează practic numărul de paleți transportați, și din 2002 a axei Rotos cu suspensie pneumatică, pentru siguranță mai mare în timpul curselor. Iar în 2006 aici s-a produs ultimul șasiu sudat Schmitz.
În prezent semiremorcile frigorifice dețin circa 90% din producție, iar cele izoterme, 10%.
Atenție deosebită și la calitate, și la respectarea timpului, și la motivarea angajaților
Pereții semiremorcilor sunt construiți pe verticală, începând de la primul panou, care se pune pe sol și peste care se așează celelalte, astfel încât mereu să se poată vedea stratul de deasupra. Panourile sunt din oțel, aluminiu sau plywood și între ele se pun circa 200 kg de substanță de lipire, iar pereții laterali asamblați împreună merg pe o linie separată de producție.
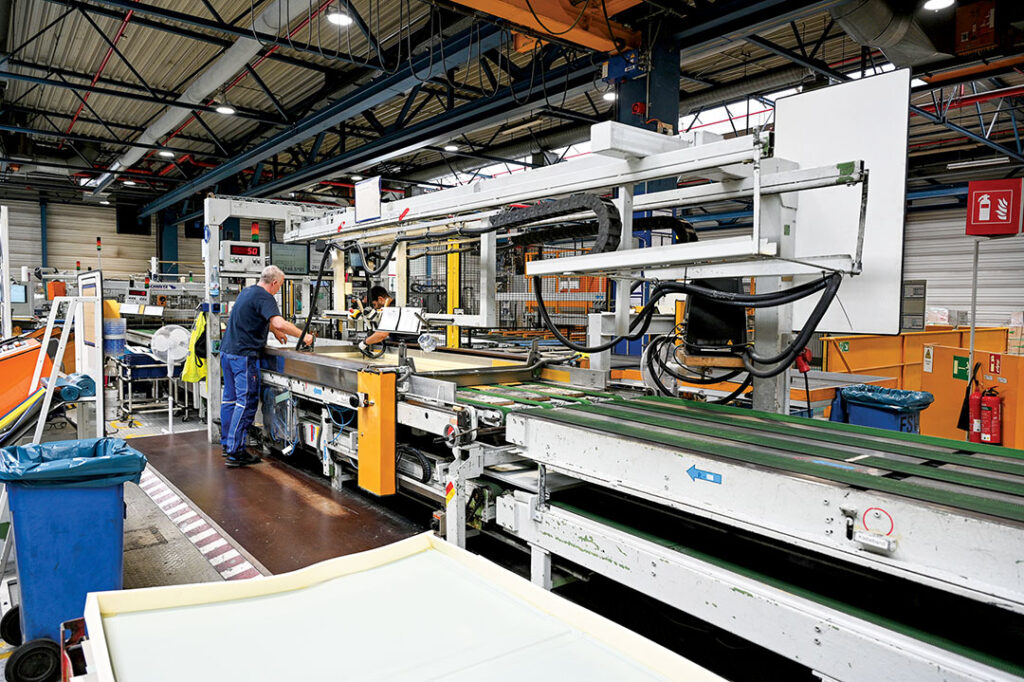
Podeaua multifuncțională (a cărei pregătire se va muta în noua hală) este alcătuită din mai multe părți și este acoperită cu o placă neagră menită să prevină daunele provocate de pietre mici, iar după finisare se aduce pe linia de producție, unde i se dau găuri pentru montarea axelor.
Pe o altă linie se produc pereții față și spate, și acesta este singurul loc din fabrică unde se face încă sudură manuală. Apoi se produc cele două uși spate care se montează manual pe cadrul spate, folosindu-se un ciocan care să garanteze potrivirea la nivel de milimetru, și după ele se montează și restul echipamentelor din spatele semiremorcii.
Pentru întărirea materialului acesta stă circa trei ore în vacuum. Iar cu ajutorul unui aparat cu laser se garantează că lipiciul nu are praf sau impurități, astfel încât vehiculele să aibă o durată cât mai mare de viață.
Panourile Ferroplast nu se reciclează, deoarece sunt compuse din două straturi de oțel care nu sunt ușor de separat, la finalul duratei de viață, de spuma dintre ele. Dar Schmitz lucrează la asta și pe viitor panourile vor putea fi reciclate într-o oarecare măsură.
La Vreden se pot produce și semiremorci mai lungi, de 13,8 m, acceptate în Germania, dar nu numai, prin adăugarea de spumă și de lemn și prin folosirea mai multor întărituri.
Componentele mici, ca șuruburile sau bolțurile, care se produc tot la Vreden, sunt astfel etichetate, depozitate și transportate încât să fie atribuite unui anumit număr de șasiu.
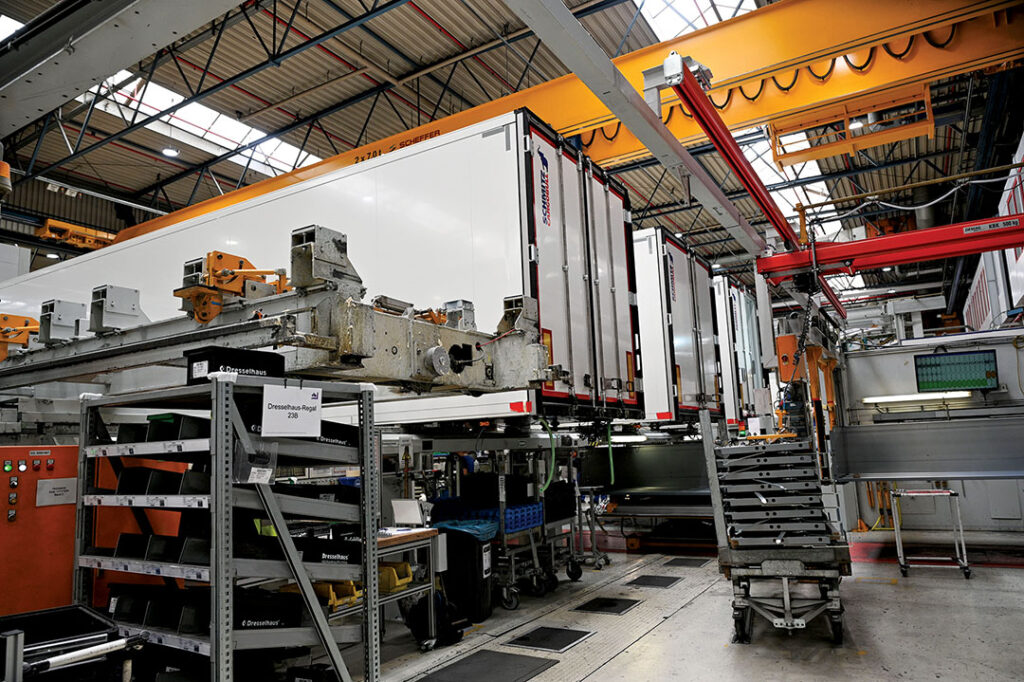
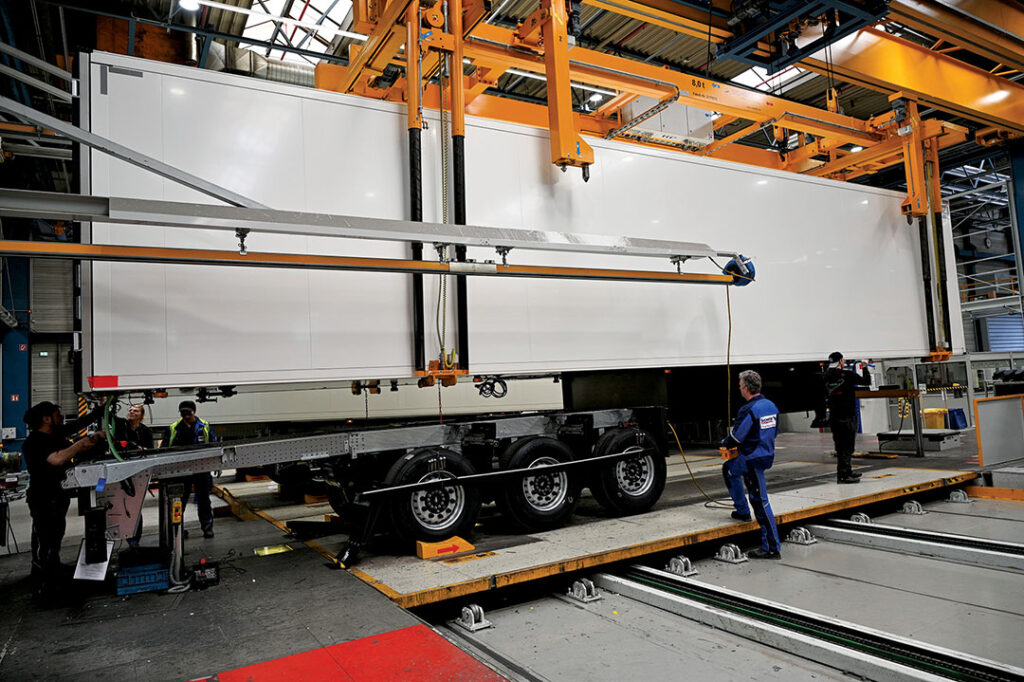
Pereții laterali, față/spate și podeaua se transportă de la o linie la alta cu ajutorul unor poduri prinse în tavan, iar sudura lor de podea, cu ajutorul unei mașini automate, se face astfel încât să garanteze că, dacă se pune apă în semiremorcă și se închid ușile, apa nu iese.
La un alt punct de lucru se face o nouă curățare a suprafețelor, se pregătesc acoperișul și instalarea cablurilor electrice, iar după montarea acoperișului se pune și partea electrică, se face o curățare totală, se pregătesc agregatul frigorific Schmitz, Carrier sau Thermo King (care vine deja setat în limba aleasă de client), cutia de paleți, dacă a fost solicitată, și alte sisteme opționale interioare – podea dublă, sisteme de ancorare, perete despărțitor ș.a. – care vin pe linia de producție just in sequence, exact pentru semiremorca pentru care sunt alocate. De altfel, fabrica nu are spații logistice mari pentru materie primă și pentru componente, deci ele vin în general direct pe linia de producție, unde nu trebuie să stea mult. De aceea se lucrează just in time sau just in sequence și de aceea este atât de important ca pe toate liniile să se respecte timpul alocat fiecărei operațiuni, iar în caz de probleme, să se intervină urgent. Fabrica dispune de un sistem de lumini ce indică în timp real cum merg lucrurile pe fiecare linie de producție, astfel încât să se poată interveni imediat la nevoie și să se respecte timpul. Lumina verde este semnul că totul se desfășoară bine, cea galbenă, că e nevoie de ajutor la un post de lucru, iar cea roșie, că procesul nu merge cum trebuie. Iar pentru ca o greșeală să nu se repete, deoarece ar costa timp și bani, angajații au întâlniri de 10 minute dimineața, în care sunt informați despre eventualele greșeli care s-au făcut, despre ce este urgent și despre ce s-a întâmplat în schimbul anterior.
În fabrica Schmitz angajații nu fac aceeași muncă întotdeauna, deoarece asta ar putea fi demotivant, câtă vreme la fiecare 15 minute execută aceleași sarcini. Ci fac anumite operații o săptămână, apoi trec la altele, iar învățarea este ușoară deoarece pentru fiecare linie de producție există specificații clare.
Tot pentru un plus de eficiență și de satisfacție a angajaților, reprezentanții Schmitz subliniază faptul că nu toate ideile menite să eficientizeze producția vin de la ingineri sau de la personalul din birouri, ci și cei care lucrează direct în producție au inițiative care să le optimizeze munca.
Revenind la producția propriu-zisă, pentru etapa finală, așa-numita nuntă – lipirea șasiului și a caroseriei și prinderea lor folosind și șuruburi mari, pentru o fixare foarte bună – șasiul este transportat cu ajutorul unor podele mobile, iar caroseria, cu podurile din tavan. La cerere se instalează manual liftul hidraulic, protecțiile față de rampa de încărcare/descărcare și echipamentul pentru tren/feribot.
Iar după verificarea frânelor, suspensiilor și sistemului telematic semiremorca este gata de livrare.
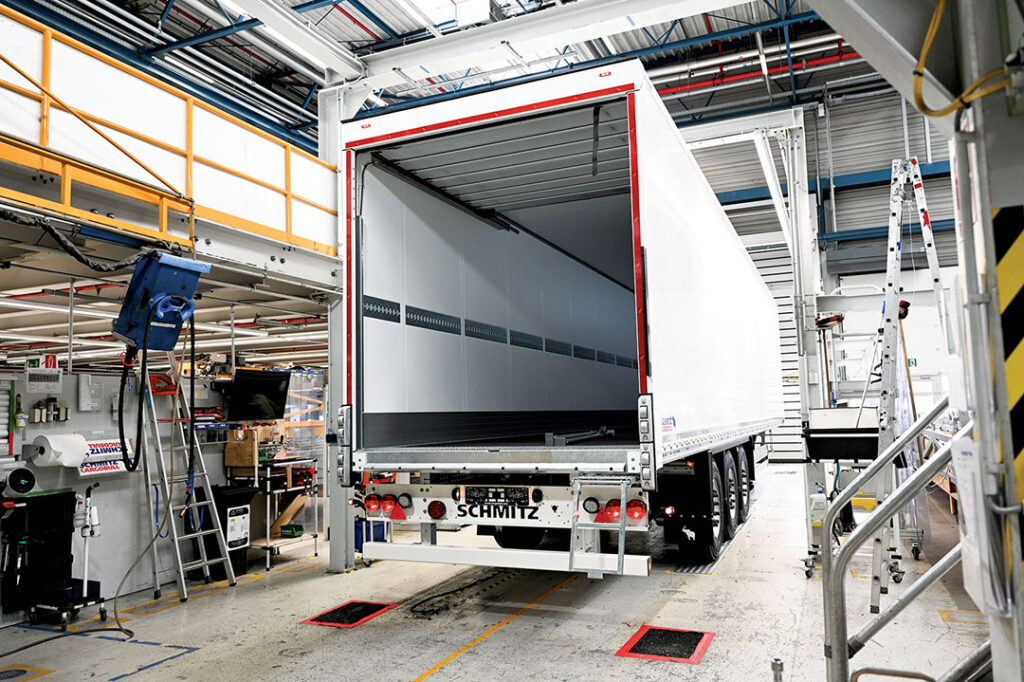
Investiții în automatizare și în creșterea producției de semiremorci și de spumă
La centrul actual din Vreden se fabrică o semiremorcă la fiecare 15 minute, iar datorită noii hale de asamblare – care va fi gata la final de 2025 sau început de 2026, va avea 4.500 m2 și o va completa pe cea actuală – se va ajunge la o semiremorcă la 10 minute, adică la 80 de vehicule frigorifice pe zi în două schimburi sau 130 de S. KO/zi plus până la 36 de S. BO în trei schimburi. Linia nouă de asamblare va fi automatizată, iar capacitatea de a produce spumă va fi și ea extinsă, pentru ca materialul să fie furnizat întregii rețele de fabrici Schmitz. Și, tot pentru întregul grup, aici va funcționa și fabrica de sisteme de iluminat Smart Factory.
Cu alte cuvinte, așa cum subliniază reprezentanții Schmitz Cargobull, se va intra într-o nouă eră în producția de semiremorci, în care posibilitățile actuale vor fi depășite cu mult.
15-20% din producția de agregate frigorifice merge în America de Nord
La circa 2 km de această locație, la Vreden-Gaxel, se află fabrica de agregate frigorifice S.CU, aparținând Cargobull Cool GmbH & Co, o filială a Schmitz Cargobull AG fondată în 2012 și care se ocupă, cu o echipă de aproximativ 100 de angajați, de dezvoltarea, testarea și producerea de agregate convenționale și electrice care echipează peste 20% din modelele frigorifice Schmitz Cargobull, procent care în 2025 se estimează că va ajunge la 30%. În prezent pe șoselele din Europa se află peste 30.000 de vehicule cu agregate frigorifice Schmitz.
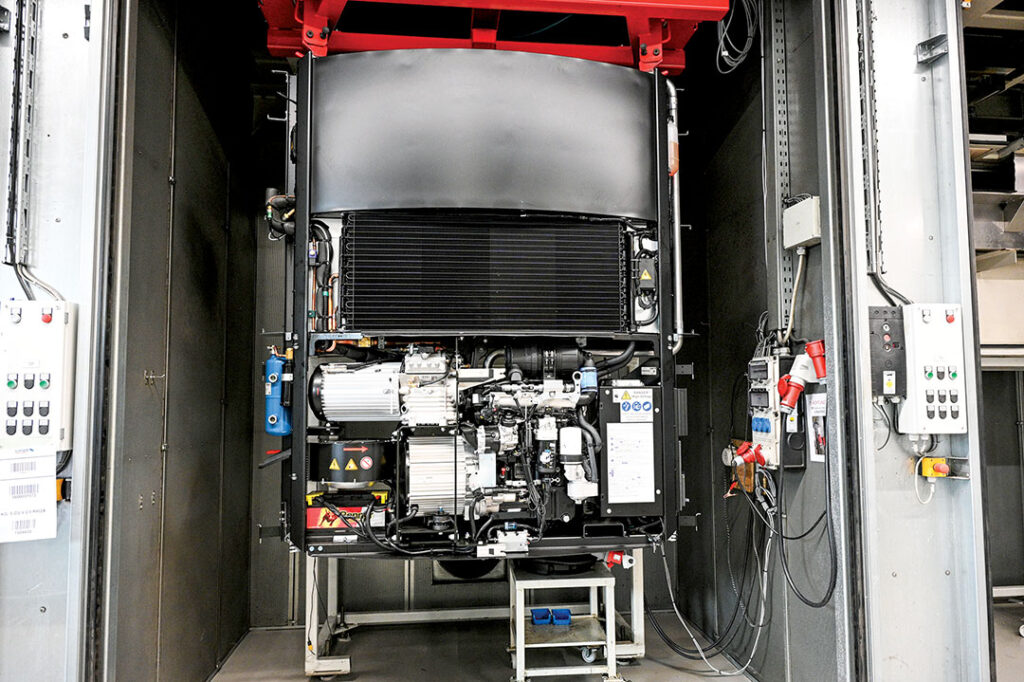
Așa cum explică reprezentanții companiei, obiectivul inițial a fost să se producă un singur tip de agregat, din gama de mijloc, adică unul care să acopere cerințele cât mai multor clienți. Dar dinamica pieței a făcut ca în 2016 portofoliul să fie extins cu un agregat multitemp, în 2019, deoarece s-au schimbat reglementările privitoare la motoarele diesel, a apărut agregatul 2.0, în 2021 a fost lansat primul agregat Schmitz complet electric, iar în 2024 a fost lansat la IAA modelul S.CU dc85.
În plus, în 2023 a fost încheiat un joint-venture cu un producător nord-american de semiremorci, care să folosească agregate frigorifice de la Vreden, astfel că acum 15-20% din producție merge acolo – unde sunt reglementări mai stricte – iar procentul continuă să crească. Și pentru piața europeană și pentru cea americană se lucrează pe aceleași linii, iar componentele sunt în general similare, dar cu unele diferențe.
Capacitatea fabricii a crescut în ultimul timp de la 11 la 18 unități într-un schimb și se lucrează în două schimburi, dar la nevoie se poate adăuga al treilea. Iar când producția scade orice angajat are pregătirea necesară pentru a lucra măcar pe 2-3 din liniile de producție.
Una dintre diferențele importante față de alți producători este că aici nu se face sudură, ci doar lipire.