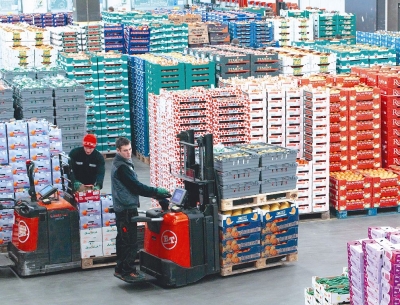
Flota de stivuitoare poate aduce economii semnificative in activitatea de depozitare, dar pentru asta analiza in vederea achizitiei trebuie sa inceapa cu procesele si, numai dupa ce nevoile firmei sunt intelese bine, se alege echipamentul cel mai potrivit
In cadrul unei cereri de oferta, multe companii comit eroarea de a face o selectie in functie de flota de stivuitoare dedicata transportului intern deja existenta. In realitate, este de preferat, in primul rand, sa fie reconsiderate procesele, pentru a determina care sunt echipamente cu adevarat necesare.
Potrivit unui raport al companiei belgiene de consultanta Wherehows Logistics, regula de baza pentru acest exercitiu este urmatoarea: in flota exista mai multe stivuitoare, insa cel mai probabil unele dintre ele pot fi scoase din uz fara a afecta fluxul operatiunilor si, de multe ori, fara vreo investitie semnificativa de capital. Intr-adevar, o analiza a proceselor poate releva ca o planificare mai atenta si o organizare mai buna sunt suficiente pentru a reduce numarul echipamentelor utilizate de o companie.
In ceea ce priveste stivuitoarele, potrivit aceluiasi raport, se estimeaza ca in mediul de productie exista mijloace de a realiza economii substantiale. Se subintelege ca optimizarea proceselor se impune si in cadrul depozitelor, dar aceasta eficientizare vizeaza in principal aplicatiile operatorilor si, implicit, economiile care pot fi realizate doar prin utilizarea eficienta a capitalului uman. In acest context, stivuitoarele sunt inlocuite de solutii automatizate, ceea ce reprezinta primul pas catre o eficienta mai mare a operatiunilor, nu o modalitate de a reduce numarul stivuitoarelor. Mai mult, transpaletii pentru pregatirea comenzilor, care sunt de departe cele mai numeroase echipamente utilizate intr-un depozit, nu reprezinta decat o parte infima a costurilor operationale.
Pentru echipamentele mai costisitoare, care ridica pe inaltime, companiile intreprind studii pentru o utilizare cat mai eficienta, de exemplu, limitand numarul modificarilor survenite asupra culoarelor sau disociind aplicatiile rezervate stivuitoarelor cu operatiuni la mare inaltime de alte sarcini de rutare a produselor, care pot fi indeplinite si de alte stivuitoare mai „traditionale“.
Transportul intern, componenta a logisticii productiei
Lucrurile se petrec diferit in logistica din cadrul unui centru de productie, unde transportul intern poate fi considerat un proces de sustinere a productiei, pentru deplasarea marfurilor intre zonele pentru stocuri tampon si cele de depozitare. In acest mediu, transportul intern este in general asigurat de stivuitoare pregatite pentru aplicatii diferite, mai costisitoare. Chiar daca accentul se pune pe eficienta productiei, se cauta oportunitati de optimizare si in plan logistic.
In multe facilitati de productie sunt repartizate echipamente pentru fiecare departament si fiecare unitate are caracteristicile si configuratia necesare operatiunilor de acolo. De cele mai multe ori se constata ca un departament dispune de un numar excedentar de echipamente, desi, cu un minimum de planificare, acesta poate fi redus.
O organizare mai eficienta a transportului intern permite companiilor sa realizeze economii de aproximativ 15%, in functie de marimea flotei si de diversitatea echipamentelor.
Un plan in patru etape
Pentru a sti daca pot fi realizate efectiv economii importante, in primul rand o companie trebuie sa raspunda la o serie de intrebari. Ce volum trebuie deplasat? De unde vin marfurile si unde se duc? Pentru ce motiv sunt deplasate marfurile? In ce moment sunt deplasate?
Daca o companie nu cunoaste raspunsurile la aceste intrebari este clar ca are niste costuri operationale destul de ridicate pentru transportul intern din depozit. Raspunsurile pot servi ca baza pentru o eventuala optimizare a operatiunilor.
Pentru a diseca procesele intr-o maniera coerenta si a detecta masurile prin care costurile pot fi reduse, compania de consultanta propune un plan in patru etape. Acestea pot fi puse in aplicare in formula completa sau independent una de cealalta.
I: Analiza fluxului de transport
Pe parcursul acestei etape, compania analizeaza relatiile de transport care exista intre departamente. La acest nivel, valoarea economiilor depinde de densitatea fluxului. Pentru a sti daca un flux de transport este dens sau nu, este suficient sa se multiplice distanta (in metri) cu numarul miscarilor zilnice. Cu cat rezultatul este mai mare, cu atat fluxul este mai dens. In practica, este imposibil sa se deplaseze fizic departamentele de productie, din cauza instalatiilor si a infrastructurii. Pe de alta parte, de multe ori este posibil sa fie deplasate doar stocurile tampon de materii prime, stocurile intermediare si chiar produsele finite. Pe anumite rute din cadrul depozitelor, echipamentele pot fi inlocuite cu sisteme alternative de transport, benzi transportoare, de exemplu, de la hala de productie catre depozitul „in-bound“.
In afara de aceasta, companiile trebuie sa calculeze fiecare miscare a stivuitoarelor, pentru a limita numarul operatiunilor „pe gol“, sau sa realizeze combinatii de doi paleti transportati in cadrul unei singure operatiuni.
Obiectivul acestei etape este, pe de-o parte, de a minimaliza distanta, iar pe de alta parte, de a maximiza gradul de incarcare.
II: Analiza stocurilor de productie
Etapa urmatoare consta in studiul posibilitatilor de a reduce numarul aplicatiilor de transport si timpul de asteptare pentru marirea stocurilor tampon pentru productie.
In practica, potrivit raportului Wherehows Logistics, s-a constatat ca operatorii nu sunt antrenati in permanenta in manipularea paletilor si ca exista frecvent timpi de asteptare intre doua aplicatii. Dar, dat fiind faptul ca intre doua aplicatii uneori timpul de asteptare este de doar cateva minute, este dificil sa calculezi capacitatea stivuitoarelor in depozit. Extinderea stocurilor tampon in productie permite cresterea marjei de timp intre doua aplicatii pentru echipamente. Astfel, lipsa unor timpi morti permite operatorului sa utilizeze stivuitoarele si transpaletii si pentru alte aplicatii in alte departamente, ceea ce duce la cresterea productivitatii in exploatarea lor. Pentru aceasta, ideal ar fi ca in cadrul fiecarei aplicatii sa se transporte mai multi paleti.
III: Analiza orelor de exploatare
Pentru a optimiza rata de ocupare a flotei trebuie determinat numarul de ore de exploatare pentru fiecare echipament in parte. Pentru aceasta etapa, este vorba de incercarea de a optimiza potentialul de a combina capacitatea echipamentelor pe mai multe linii de productie sau chiar mai multe departamente.
Potrivit raportului, la ora actuala, echipamentele sunt de multe ori alocate catre departamente specifice. Dar cand nu exista nimic de facut acolo, ele sunt in stand-by.
Prin dezvoltarea unui plan detaliat de utilizare a echipamentelor, pe ore de exploatare pentru fiecare proces, prin combinatia unei linii de productie si a transporturilor corespondente, se poate obtine o valoare mai buna a gradului de exploatare a flotei si posibilitatea de a folosi echipamentele si in alte departamente. Fie ca sunt utilizate pentru productie, fie in depozit, este important sa ai un raport complet din care sa rezulte contributia la eficienta operatiunilor a orelor in care echipamentele sunt in miscare. Pentru a afla gradul de eficienta a unui echipament se face o comparatie intre numarul de miscari realizate si volumul prevazut.
IV: Analiza flexibilitatii
La final ramane de analizat configuratia necesara pentru fiecare echipament.
Potrivit raportului, in practica s-a dovedit ca stivuitoarele sunt adaptate tehnologic la aplicatiile pentru care au fost achizitionate. Asta antreneaza o mare diversitate a configuratiilor si specificatiilor tehnice pentru un parc dedicat aceluiasi tip de marfa si acelorasi operatiuni.
Asigurand un grad cat mai inalt de uniformitate flotei, sau, mai bine spus, alegand echipamentele care pot asigura un numar cat mai mare de operatiuni, se poate obtine un plus de flexibilitate in repartitia echipamentelor pentru anumite aplicatii. Aceasta flexibilitate asigura avantaje atat pe termen lung, cat si scurt: in cadrul operatiunilor cotidiene, permite schimbarea mai facila a echipamentelor in cazul unor variatii ale volumelor sau defectiuni, iar pe termen lung creste nivelul de interschimbabilitate a stivuitoarelor, pentru exploatarea din plin a acestora pe toata durata de viata, si implicit o reducere a costurilor de capital.
In timpul primilor ani de viata, echipamentele noi sunt utilizate mai intens, iar apoi servesc unor sarcini mai putin solicitante, cu un numar relativ mai mic de ore de exploatare pe an. Avand ca scop o mai mare uniformitate la acest nivel, se pot crea posibilitati de a opera un volum mai mare cu o flota mai mica de echipamente.
Pentru a pune in practica acest plan si a lua masurile necesare, companiile pot optimiza operatiunile pentru fiecare stivuitor sau transpalet fara interventii drastice in organizarea logisticii. O planificare inteligenta este cel mai bun mijloc pentru a realiza economii.
Scurtarea distantelor de transport, cresterea gradului de ocupare, schimbarea echipamentelor si netezirea varfurilor de activitate reprezinta calea cea mai rapida pentru diminuarea volumului total de munca. Iar prin reducerea volumului de munca se intelege un timp mai scurt de exploatare a echipamentelor si implicit costuri reduse atat de exploatare, cat si cu forta de munca.
O companie poate decide sa pastreze un echipament pentru care investitia s-a amortizat complet, ca solutie de back-up pentru varfurile de activitate si pentru a oferi flexibilitatea de care este nevoie in anumite perioade cu volume mai mari de operat.
Conform raportului Wherehows Logistics, in depozit este mai bine sa se opteze pentru echipamentele standard, capabile sa manipuleze toate tipurile de marfuri, dar care sa garanteze cea mai buna solutie de interschimbabilitate a flotei.